How to make a backlit plasterboard ceiling
One of the most dramatic design tricks is the use of lighting effects. Often it is the light that gives the interior a zest. A backlit plasterboard ceiling is one of the most common options. It is good because, if you wish, you can do it yourself, with your own hands.
The content of the article
Main design differences
The backlighting of the plasterboard ceiling is hidden and open. Open - spotlights that are fully or partially visible. The hidden one is called so because only its radiation is visible. Therefore, when installing a plasterboard ceiling with hidden illumination, the lower level boxes are made with a shelf on which the lighting fixtures are placed.
This shelf can be open or closed and, depending on this, and the position of the light sources changes the width and brightness of the strip of light on the ceiling.
Backlight box design
To make such a box for lighting the ceiling, you need two types of profiles:
- UD - guides. They are mounted on the ceiling and on the wall, also in the middle of the structure and at the point where the side is attached, if provided.
- CD - bearing profile of greater rigidity. Racks and lintels are made of it, to which the plasterboard sheet is attached.
In the variant shown in the photo above, the shelf does not rest on anything. The rigidity of the gypsum board itself is enough to keep the light backlight. In this case, the weight of the lighting elements must be taken into account. The heaviest are fluorescent lamps, but they have practically not been used recently, since there are other options that are more economical in energy consumption and easier to install (LED strips, duralight).
There is a second construction. Here the extension of the shelf rests on elongated cross members. If the previous construction seems unreliable to you, you can do this. Only in this case a little more bearing profile will be required. The photo shows an example of the organization of a two-level flow from drywall with backlight.
The exact same scheme can be implemented in a single-level version. If your main ceiling is in good condition, you can only make a perimeter box. An example of an assembled framework for lighting is below. It remains to make an inner side, and hem the frame from below.
A backlit plasterboard ceiling does not always have straight lines. They are simply the easiest to implement. But the same patterns are done with curved lines. The result is very beautiful false ceilings.
Only at large distances from the load-bearing walls, it is necessary to additionally fix the load-bearing profile either to the ceiling or to the profiles of the previous level. It is more convenient to do this with suspensions.
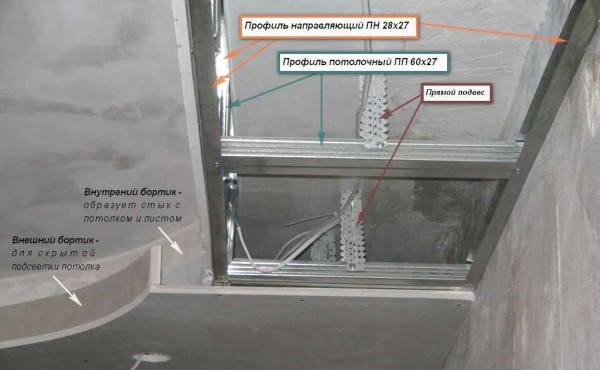
With a large width of the backlight box, the supporting profiles are additionally fixed with hangers
Sources of light
When planning to make the illumination of plasterboard ceilings, one must remember that this is not lighting at all, but only a way to decorate the room. The stream of light is diffused. Initially, it is fused onto the ceiling, and then into the room. And it adds almost nothing to the overall illumination of the room.With its help, you can visually "raise" the ceiling, make it one of the components of the interior, but this element cannot be considered lighting. You will have to take care of lighting separately: install built-in lamps, wall or traditional - chandeliers.
Backlighting can be done using different light sources, but recently three types have been used:
- LED
- tapes;
- duralight.
- Neon tubes.
LED strips and duralight
This is a series of LEDs in series. Their peculiarity lies in the fact that they are powered from 12 V or 24 V. This power can be provided using an adapter that converts the voltage of a 220 V household network into a lower one. There are monochrome ribbons (white, red, blue, green) that are designated SMD or universal RGB when marking.
Monochrome always emit one color, the color of universal ones can vary. RGB tapes work only with a controller and remote control. On command from the control panel, they change the hue (the number of colors can be different - from tens to hundreds), in some models the intensity of the glow can also change.
By the type of execution, LED strips are:
- Ordinary. They do not have a protective coating and can only be used in dry rooms.
- Waterproof. Their surface is covered with varnish. Can be used for lighting wet rooms - kitchens, bathrooms.
- Moisture resistant. Sealed in a polymer tube (called duralight) or housing. They are rarely used for room illumination, more often in aquariums, swimming pools, etc.
The choice is clear. Select the type of tape depending on the room conditions. More details about types, colors, marking, connection can be found here, and we will talk about the good or bad LEDs in the backlight.
First, about the advantages:
- Low power consumption. They are very economical. Considering that this is only decoration, I don't want to spend large sums on its content.
- Do not get warm. Only the power supply can get warm, the LEDs themselves do not heat up. This is important if the ceiling is wooden.
- Long service life. Counts in thousands of hours. Under normal power supply, they burn out very rarely (do not exceed the current for which they are intended).
- Low price. SMD 35 * 28 tape 5 meters long and 120 pcs / m density costs about $ 2-3. Approximately the same should be paid for the adapter. True, these are the prices of Aliexpress. In stores, everything is much more expensive (2-3 times), although you will not go broke either.
- Simple installation. An adhesive composition is applied to the back surface of the tape. Remove the protective layer and stick in the right place. If the surface is rough, you can "shoot" with staples from a construction stapler, but it is better not to punch the tape itself.
Now about the disadvantages. First, and most important: LEDs firmly illuminate all surface flaws. Therefore, the requirements for the quality of the ceiling finish are very high. Second disadvantage: the presence of adapters. They need to be attached somewhere. Probably that's all.
Neon tubes
These are glass tubes filled with a mixture of inert and luminous gases. The brightness of the glow changes when the current strength changes, which is regulated by the convector. These devices are installed every 5 meters, their power consumption is about 100 W, they do not make noise during operation.
Also, a step-up transformer is needed for operation: normal voltage is not enough for neon to work. Transformers are installed every 6 meters. But they can hum during work, and also - warm up and electricity, of course, "pulls" pretty well. The entire system as a whole consumes a fairly large amount of electricity, which, together with the fragility of the tubes and the rather high complexity of installation, makes it not very attractive compared to LEDs.
But recently neon cords have appeared. They come immediately with a controller and all you need is to press a button. They work from AA batteries.But the power of such illumination for the ceiling is definitely not enough. They can be used in conjunction with LEDs to illuminate interior details.
Installation of ceiling lighting around the perimeter with step by step photos
The main ceiling in this version was putty, therefore the first tier was not done. Only the box was attached around the perimeter: the height is already small and 7-8 cm required for the organization of the suspended one are critical.
There is a place for the cornice near the window, the width of the box is 60 cm, it is lowered by 12 cm relative to the main ceiling, the height of the side is about 5 cm, the protruding part is 6 cm, roundings are made in the corners.
The first method was chosen - a step under illumination without support. Since the backlighting is planned from a conventional LED strip, its carrying capacity is more than enough.
First, markings are made on the ceiling. All the specified dimensions are set aside, lines are drawn with the help of a paint cord. Please note that the line on the ceiling is laid at a distance of 54 cm, and not 60 cm, as in the first diagram. It is obtained taking into account the fact that the step is pushed forward by 6 cm.
When drawing rounds, their center is made not in the place where the profile is attached, but taking into account the protruding step: this way the element turns out to be more expressive.
Profile guides are attached along the marked lines (CD or PNP in the marking). Fastened to dowels with a pitch of 50 cm. Drilled immediately through the metal. Having installed the plug, the dowel-nail was twisted.
Where it is necessary to form a rounding, the walls (sidewalls) of the profile are notched, the back remains intact. After that, the profile can be laid out in a circle.
From the front side to the guide profile on the ceiling, we attach a strip of drywall 12 cm wide.This will be the rear side of our box. We fix it around the entire perimeter with self-tapping screws with a screw at a distance of about 10 cm.
On the back side of the installed side, we attach vertical posts from the CD profile (ceiling). Their length is small - 9.8 cm (12 cm box height, minus 1 cm for the installation of profiles, and another minus 1.2 cm for the thickness of the gypsum board screwed from below)
In each section, the bottom is trimmed. The side walls are removed so that another guide profile can be screwed on. As a result, its bottom shelf should be flush with the profile bolted to the wall. The installation step of the vertical racks is about 40-50 cm.
The next step: we fasten the PNP profile, which goes along the bottom of the boat. It is also installed on self-tapping screws with a pitch of 10-12 cm.
Next, we proceed to the installation of horizontal jumpers, on which the GKL sheet will be held, closing the box from below.
They connect two guide profiles: the one that is screwed on the wall and the one that is attached to the main board. They are made from a supporting profile with a step of 40-50 cm.
We proceed to the design of the roundings. In order for the strip to bend along the required trajectory, we take a strip of drywall about 15 cm wide.Cut it in 5 cm increments and break the gypsum. The result is pieces of plaster that stick to the cardboard.
Now we attach such pieces to the profile. For each fragment - one self-tapping screw, approximately in the middle of the width, so as not to burst.
Using the laser level, transfer the height markings to the inner side. If there is no laser level, use water and draw a line with a pencil.
Then we take a piece of the bearing profile 9.8 cm long, only we cut it off from above and below.Approximately in the middle of the arc we wind one edge behind the profile, fasten it with a self-tapping screw.
Then we take a piece of the profile cut into fragments (as they did when forming a circle on the ceiling) and fasten it along the mark.
Now the extra pieces of plasterboard can be removed. They are cut to the level with the lower edge of the profile, carefully cutting the paper and breaking off small fragments.
The next step in making a backlit plasterboard ceiling is putty. The ceiling and the main side are putty. This is the most convenient moment for this. Later, the bottom hem and the protruding cornice will interfere.
Next, we begin to hem the box from the bottom. Strip width - 60 cm. Cut and fasten with self-tapping screws. The procedure for working with gycardboard is standard. Some explanations are required only for sewing corners.
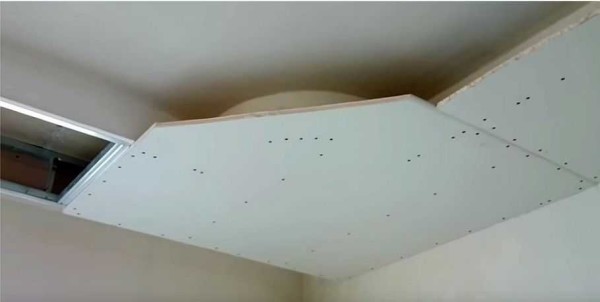
We fasten the sheet, which fits well into the corner and is slightly larger than the required rounding in outer dimensions
The most convenient way is to cut a square, then cut it on one side. First, we screw it in straight lines. Then, gradually, in an arc, drawing the required edge shape.
First you can draw, then bite off in small pieces along this line. Smooth out irregularities with a wallpaper knife.
Next, we fasten the guide profile. An additional side will be attached to it, which will cover the backlight.
No news: for the roundings, we cut the sidewalls, bend them with the desired diameter and set them in place, fixing them with self-tapping screws.
If you are planning to make LED lighting for your plasterboard ceiling, it's time to fix the tape. Then it will be very uncomfortable. It is glued in the right place, if necessary, setting some kind of inclined plane.
Further, a strip of drywall 5 cm wide is attached to the profile. Of the features - fastening in the middle, and not above and below: the height is too small. Bends are also familiar. We cut a strip every 4-5 cm, break the plaster and fasten it.
In this version, in order to facilitate the work and give the ceiling a finished look, fillets are glued to the side (ceiling plinth). Similar ones are glued at the junction of the box and the wall.
Now it remains to putty everything and achieve a flat surface. Almost everything. The backlit plasterboard ceiling is ready, it remains to install the backlight itself. And it can be different.
Another option can be seen in video format, but with a working backlight.
The installation of a bi-level stream is demonstrated in the following video. The steps are shown schematically, but the assembly of the first level is clear. So that might be helpful.
How can you arrange a plasterboard ceiling with lighting (photo)

LED lighting of the plasterboard ceiling is only a spectacular design technique. Lighting needs to be taken care of separately