Choosing electrodes for a welding inverter
For a novice welder, the choice of an electrode can be a problem: there are more than two hundred brands with different properties, purposes and characteristics. Moreover, about 100 brands are suitable for manual electric arc welding with inverter machines. It is impossible to tell about everyone, yes, to begin with, it is not necessary. Let's just briefly describe the main types and which electrodes for inverter welding are most suitable for beginners. We will also talk about what diameter to take and what current to set for welding metal of different thicknesses.
The content of the article
What is an electrode and what is coating for
An electrode is a piece of metal wire coated with a special coating. During welding, the core melts from the arc temperature. At the same time, the coating burns and melts, creating a protective gas cloud around the welding area - the weld pool. It blocks access to oxygen in the air. In the process of burning the mixture, part of it turns into a liquid state and covers the molten metal with a thin layer, also protecting it from interaction with oxygen. So the coating ensures a good weld quality.
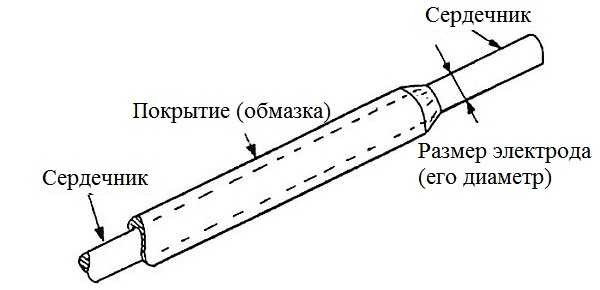
The welding electrode consists of a core and a protective coating
Before starting welding, any electrode is inspected: the coating should not have chips. Otherwise, you will not achieve uniform heating and a high-quality seam. Also, pay attention to the tip of the electrode: the thickness of the coating should be the same on all sides. Then the arc will come out in the center. Otherwise, it will be displaced. For experienced welders, this is not scary, but for beginners it can create tangible problems.
It is necessary to monitor the moisture content of the coating. Some of them ignite very poorly in high humidity (for example, SSSI). In connection with such a "capriciousness" of the coating, they must be stored in a dry place, providing, if possible, hermetic packaging. You can put the box in a bag, and also put a few bags of salt there, which are in shoe boxes.
It is not worth buying wet electrodes: they can, of course, be dried, but their characteristics will decrease. If, nevertheless, it so happens that the electrodes are damp, they can be dried in an ordinary household oven at low temperatures (they are usually indicated on the package). The second way is to put it in a dry, well-ventilated room for a long time.
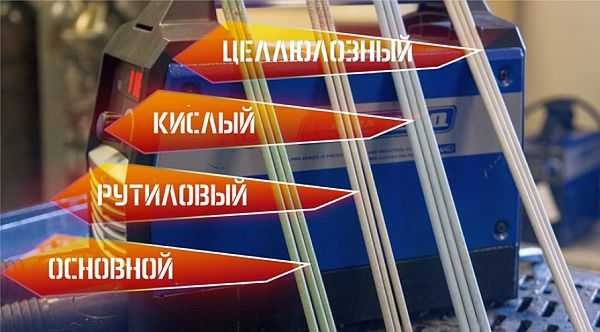
The coating (protective coating) of the electrodes is: basic, rutile, cellulose and acidic
Types of coating and their characteristics
There are only four types of coatings:
- Basic.
- Rutile.
- Sour.
- Cellulosic.
Basic (SSSI) and cellulosic coatings are only suitable for DC welding. They can be used on critical seams: they create a strong, elastic seam that is resistant to shock loads.
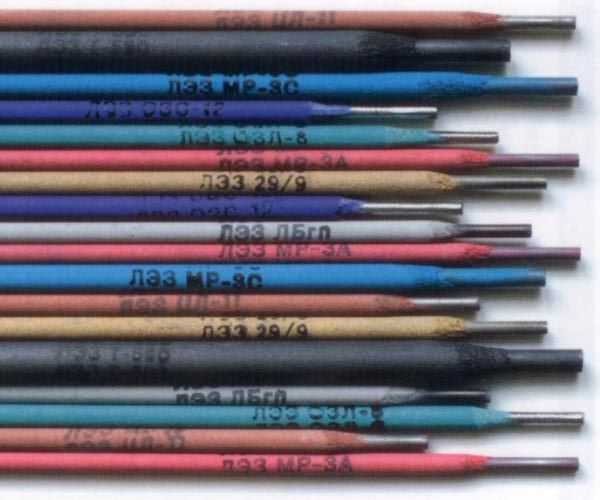
There are more than 200 brands of electrodes for welding, about 100 of them can be used for manual electric arc welding
The other two (rutile and sour) - can work when welding with alternating and direct current. But the acidic coating is very toxic: you can work indoors only if the workplace is equipped with a forced draft.
Rutile coating has a greenish or blue tint, the electrodes are easy to ignite. They ignite well even if the inverter has a low open-circuit voltage (for reliable ignition of the main coating, a good current-voltage characteristic is required, how to choose an inverter welding machine, read here.).When welding with rutile electrodes (MP-3), the metal hardly splashes, but there is a lot of slag and it is not easy to come off: you have to work with a hammer.
You might be interested in how to weld a gazebo from a metal pipe or how to make a shed on a frame from a pipe.
How to choose electrodes for inverter welding
First of all, the composition of the core is selected: it should be similar to the type of metal being welded. In households, structural steels are most commonly used. It is from the same wire that the electrodes should be. Sometimes you still have to cook stainless steel. Then the core must also be made of stainless steel, and for high-alloy and heat-resistant ones they are made of metal with the same characteristics.
You can perform all housework or construction work using just a few brands of electrodes:
- MP-3
- SSSI 13/55
- ANO 21
- OK 63.34
They are recognized by many as the best newbie electrodes that work with inverter welding machines: it is easier to work with them, at the same time, they allow you to cook high-quality seams, even in the absence of significant experience. Below are the characteristics and general applications of those consumables that many experts consider to be good electrodes for an inverter. In any case, they are often recommended for novice welders to gain experience.
Rutile coated electrodes MP 3
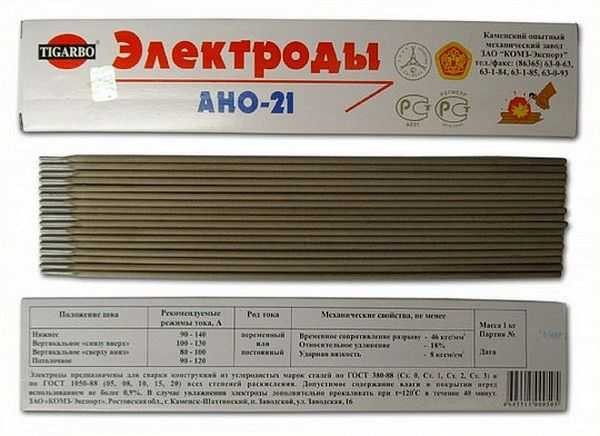
Try ANO 21 electrodes for operation on the inverter
They work with both alternating and direct current of any polarity. Heat treatment is required before welding: they are calcined at 120 ° C for 40 minutes.
Diameter, mm | Lower electrode position | Vertical position of the electrode | Overhead electrode position |
---|---|---|---|
2 | current strength 50-90 A | current strength 50-70 A | current strength 70-90 A |
2,5 | current strength 60-110 A | current strength 60-90 A | current strength 80100 A |
3 | current strength 90-140 A | current strength 80-100 A | current strength 100-130 A |
Stainless steel electrodes OK 63.34
If you need to weld stainless steel, try OK 63.34. They can also be used to cook structural steel. This results in a seam with a shallow wave with a smooth transition to the main surface of the metal. The amount of slag is small, beats off easily.
It is good to cook with this electrode vertical seams in metal 6-8 mm, passing from top to bottom. Suitable for multi-pass butt and lap welding. Operates with direct and alternating current of any polarity, minimum open circuit voltage - 60 V.
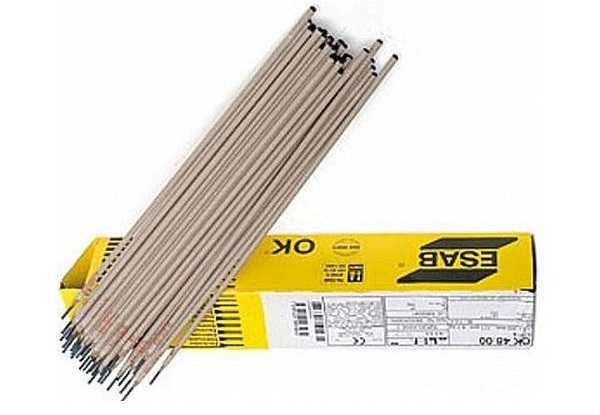
Welding electrodes OK 63.34
You also need a mask for welding. To make it easier to work, take chameleon welding mask.
How to choose the diameter of the electrode, how to connect it and which one to set the amperage
Choosing a brand of electrodes for the inverter is not all. Even if you've made up your mind, at least three questions remain:
- what diameter of the electrode to use when welding;
- what current to set;
- to which output "+" or "-" to connect the electrode.
Everything in order. Let's start with what diameter of the electrode is needed for welding. In general, it is recommended to proceed from the thickness of the metals being welded: for small thicknesses, the electrode is taken with a diameter of the same size as the metal. If you are welding metal 3 mm thick, then the electrodes are of the same size. If you cook something thicker, take 4 mm accordingly. But it will be difficult for beginners to work with large electrodes. Start mastering welding with a metal thickness of 3-4 mm. To do this, use electrodes 3 mm, or as they say "three".
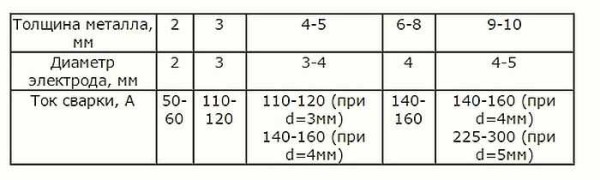
General recommendations for choosing the diameter of the electrode depending on the thickness of the metal
Regarding how to which output to connect the electrodes. The specifications on the pack most likely indicate which polarity the electrode is intended for. When connected back to the positive output, connect the electrode to the negative terminal, which is hooked onto the part. With straight polarity, a plus is planted on the part, a minus is applied to the electrode. How it looks on a welding inverter is shown in the photo.
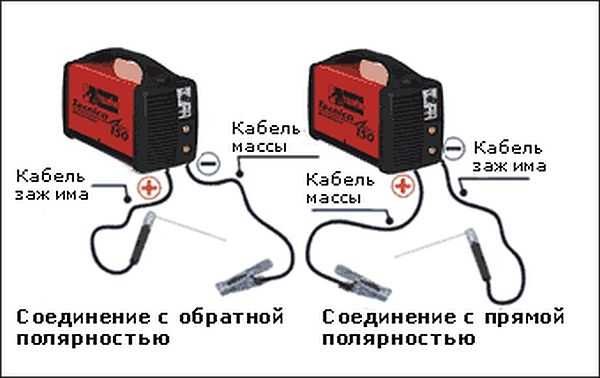
Forward and reverse polarity of connection on the welding inverter
How are these two connection types different? The flow of electrons has a different direction. As you know, electrons move from "minus" to "plus". Therefore, when welding, it turns out that the element that is connected to the "+" heats up more. By changing the connection modes, you can control the intensity of metal heating.
Let's consider several situations. For example, you have a 3 mm electrode and 2 mm metal. If "+" is applied to the part, burnout may result. Therefore, in this case, it is better to use reverse polarity, at which the electrode will heat up more. If you want to weld 6 mm metal with the same three, it is better to do this on straight polarity: this way the heating of the metal will be deeper and the seam will be more durable.
How to choose an inverter welding machine read here... May interest you construction of a fence from corrugated board.
Welding current
In general, when installing the electrode, the welding current for the inverter is set depending on the diameter of the electrode used. In general, there are recommendations on each pack, but you can do without them: for every millimeter of diameter, they take 20-30 Amperes of current. It turns out a fairly wide range, but then you still need to take into account how you will lay the seam: with or without separation. For welding without separation, lower currents are set, with separation - higher.
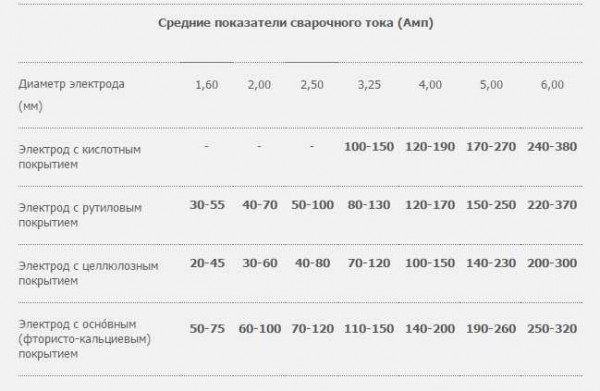
What current should be cooked with different electrodes (general recommendations, choose exactly empirically)
For example, for an electrode with a diameter of 3 mm, the calculated current is obtained from 60 A to 90 A. In reality, they work in the range from 30 Amperes to 140 Amperes. When welding without separation, a current of about 70-90 A is set, with a separation of 90-120 A. These parameters can "walk" in both directions: it also depends on the speed of movement of the electrode tip, on the brand and "fluidity" of the steel being welded, on the position of the seam (for a vertical and horizontal seam, they put a little less, for a ceiling - even less).
In general, even the currents recommended by the manufacturer are far from a requirement. Start with them, and then choose so that it is convenient for you to work and the seam turns out to be good. You should get a high-quality connection, and you will choose the ratio of current strength and speed of movement experimentally. In doing so, be guided by the condition of the weld pool. She is your main indicator of quality.
About how to cook with inverter welding read here.
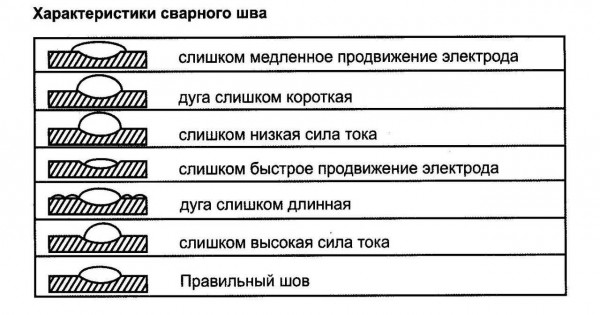
Errors that can occur when welding
Now you know not only how to choose electrodes for inverter welding, but also how to connect them, what diameter they need for this work, and how to select the current for each type of electrode and seam. Now let's talk a little about the electrode holders.
Holders for electrodes
One of the welding cables has a holder (holder) into which the welding electrode is inserted. They are of two types:
- with a trigger key, the electrode is automatically clamped in them when the spring-loaded key is released, it is released when it is pressed;
- threaded - the handle is twisted and untwisted, releasing or clamping the inserted electrode core.
Which one is better? It's up to you, but by accidentally pressing the button, you can drop the electrode during welding. Nothing terrible happens with this, but it's unpleasant ...
When choosing an electrode holder, the main thing is to pay attention to the current strength for which it is designed. Choose according to the maximum parameter that is available for your welding machine.
How to connect the cable to the screw clamp welding electrode holder is shown in the video.
The disadvantage of the clothespin holder is that from time to time the spring pressing the electrode core loosens, the contact deteriorates. We have to put a new one. How to do this on a clothespin holder, see the video.
It is not difficult to connect the electrode holder for welding. There is only one caveat: with frequent work, the welding cable is frayed with its edge. You can, of course, shorten the cable and reseal it, but you don't always want to cut off even 10-20 cm.To prevent this from happening, find a hose whose inner diameter is the same or slightly less than the outer diameter of the welded cable. Cut a small piece of it - 15 centimeters - and cut lengthwise. Now it can be put on the cable, pulled up and fixed there.
Hello. Well written article, straight step by step about different types of electrodes. Which are more in demand. I would like to add from myself. Little bit. To be honest, LEZ MP-3S electrodes do not cook badly, in different positions. But the welding process is not soft, but rather of medium hardness. But the LEZ ANO-21 electrodes are cooked softer, they are re-ignited better. My opinion is not a pro, but rather a self-taught welder 🙂 My conclusions are just an outside opinion. I cook with an inverter welding machine Rilon Profi ARC 200 A. Welding I recommend for beginners who decide to start welding 🙂
Simple, accessible and from oneself, and not torn off somewhere.
Council.
Add a sentence: "I liked it, don't forget to turn off the ad blocker and click on gogle +, etc.".
Such sites need to raise the rating, and many will simply leave after reading it.
Good article. For beginners, this is enough. Inverter, mask, electrodes are purchased. Scraps of unnecessary metal are also available. Only the electrodes we sell are only Chinese. Everyone boils, they don't complain. I'm waiting for the weekend, going to the dacha and with the help of this article I start training.
I read many different articles. This is one of the rare content. Thanks to the author.
I have a Fubag IQ 200 apparatus. The electrodes were found by "Resanta" MR-3 3 mm.
I'm a newbie.