Flat slate: pressed and unpressed, sheet size, installation
No matter how much money is saved, it is always not enough for repair and construction. In the process, the question often arises about inexpensive, but high-quality, reliable and durable materials. It is very rare to find an option that meets all of these criteria. But one of these is flat slate. This material is also called asbestos-cement slab, aceite (correctly "ACEID"), chrysotile cement sheet or slab.
The content of the article
What slate is made of
Slate sheets are made from a mixture of cement (80-85%) and asbestos fibers (15-20%). A little water is added to the mixture, rolled through rollers, forming a layer of the required thickness. Further, the excess is cut to size. That is, slate is concrete reinforced with asbestos. It can also be called an asbestos-cement material. According to the old GOST, flat slate was called "asbestos-cement slab". Partitions of the bathrooms are made of it in many old buildings. So the material is proven over the years.
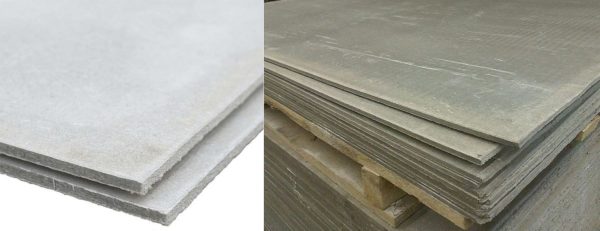
Flat slate is a cement to which a reinforcing agent, chrysotile, is added. In the new standard, it is described as chrysotile cement sheet
Many people fear the harmfulness of slate, since asbestos fibers are used as a reinforcing element. But asbestos is the general name for a group of substances. This group contains both harmful (amphibole asbestos) and neutral substances - chrysotile. Chrysotile is used in the production of slate. This requirement is spelled out in the standard and there is no need to violate it, since it costs no more and has good characteristics.
Pressed and unpressed: what is the difference
Speaking specifically about smooth or flat slate, there are two types: pressed and unpressed. The thing is that the sheets formed from the wet mixture "reach" the desired moisture content in two ways. The first is that they simply gain strength in natural conditions, like ordinary concrete. They are kept in chambers with a certain level of humidity to gain strength, and then dried. The second way - the formed sheet is pressed and then aged for curing.
How does pressed flat slate differ from unpressed as a result? With an equal sheet thickness, the pressed has:
- Greater density, higher strength. For example, 23 MPa versus 18 MPa.
- Better shock resistance.
- Higher frost resistance. But here it must be borne in mind that after the exhaustion of the resource, it quickly loses its properties - up to 40% of the original value. Non-pressed is designed for fewer defrost / freeze cycles, but after the resource is exhausted, its strength decreases slightly - by 10-15%.
- Pressed sheets have better geometry.
- It costs more, since additional equipment is involved, because of this, the energy intensity of production increases.
In general, if the material has to withstand loads, you can either take unpressed, but thicker, or pressed. Also pay attention to frost resistance. The higher it is, the longer the flat slate will last.
Properties, disadvantages and advantages
Slate was invented over 100 years ago. The technology for its production is simple, the material is inexpensive, and the properties are very good:
- Flame retardant. Does not burn and does not spread combustion.
- Environmentally friendly.
- Easy to assemble.
- Well processed (cut).
- You can work in any weather.
- It can be large, since it does not weigh very much.
- Resistant to aggressive environments.
- It tolerates atmospheric and temperature influences normally.
The disadvantages include the inconspicuousness of the "basic" version. Few people like gray material today. There are, of course, dyed in mass or paint. But for the price they are more expensive. Although, there is always an option - to paint it yourself. Another disadvantage of flat slate is poor tolerance of point loads. If you hit the sheet, it will split. Another point - it does not hold long-term bending loads poorly. Therefore, when making slate fences, the sheets are not fixed rigidly, but through gaskets so that it is possible to compensate for the resulting stresses.
Dimensions and weight
The requirements and characteristics of flat slate are defined by the new GOST 18124-2012. First, the sheets of flat slate should be rectangular. The permissible deviation is no more than 5 mm on one face. Deviation from the plane - 4 mm for pressed, 8 mm for unpressed. Second, the edges must be straight. There may be a slight bevel - no more than 5 mm.
The same normative document defines the dimensions of flat slate:
- Sheet length can be 1200 mm, 1750 mm, 2500 mm, 3000 mm, 3600 mm. Permissible deviation ± 10 mm.
- Sheet width 1120 mm, 1200 mm, 1500 mm, 1570 mm. Possible mismatch with declared width ‡ 6 mm.
- The thickness of a flat slate can be from 4 mm to 40 mm, but this is by agreement. The following values are defined by the standards:
- 6 mm and 7 mm (deviation +0.7 mm or -0.2 mm);
- 8 mm, 10 mm, 12 mm (can be 1 mm thicker, 0.6 mm thinner).
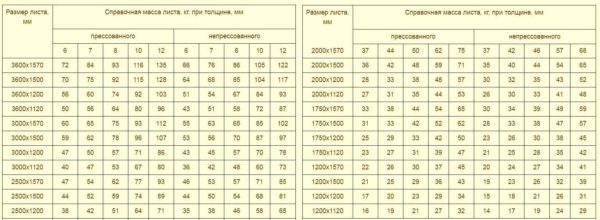
Approximate weight of a sheet of flat slate, depending on dimensions, thickness and production method
The weight of a sheet of flat slate depends on its density, production method (pressed or unpressed) and dimensions. The standard provides reference data for the sheet weight of each of the formats described. As you can see from the table, pressed, with the same dimensions, weighs 5-10% more.
Scope of use
Flat slate can be used very widely. Compared to other sheet materials, it has a low cost, and the characteristics are not bad. Smooth sheet slate is used:
- For wall cladding inside and outside buildings. The purpose of the buildings is any. The standard allows the use of asbestos-cement flat sheets in residential, administrative and industrial buildings.
- For filing the ceiling.
- For cladding ventilated facades.
- As a removable and non-removable formwork for concrete work.
- With a dry floor screed, laying on a rough floor covering under tiles.
- For roofing.
- In the production of sandwich plates.
- For fences.
- For fencing balconies and loggias.
- For the device of household and utility buildings: for summer shower, sheathing of sheds.
- When device high beds, planning of beds and other work on the improvement of the site.
In general, flat slate is one of the most affordable sheet materials that can be used in high humidity conditions or outdoors. It can look quite presentable, since there is not only gray, but also dyed. Moreover, there is dyed in the mass, there is - after production. Dyed in the mass and on the saw cut / chip has the same color. The colorant is added to the mixture prior to sheet forming. The color is more stable, but it is not bright, since the basis of the material is Portland cement.
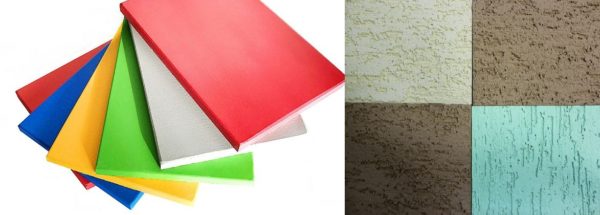
Factory painted flat slate can be glossy or matte. For finishing facades, they began to make a coating of textured plaster
The dyed finished sheet slate has brighter colors. It also happens with a glossy surface.But in places of cuts / cuts / chips, the original gray color is visible. To improve aesthetics, it is advisable to tint the sections.
You can paint the slate yourself. There is a special paint for slate, but paint for concrete is also quite suitable (after all, slate is, in fact, the same concrete). You can use enamels or acrylic paints, but you need to look so that they can be painted on concrete / cement.
Installation features
Most often, flat slate is attached to the crate with nails or self-tapping screws, screws. There are special nails - slate. They have rather large rounded caps. The nail shank can be regular or polished. The latter are used if the region has high wind loads. You can also use roofing screws. They can be painted or you can paint the hats yourself. It is very important not to tighten the fasteners all the way, but to leave some freedom of movement. This will reduce the possibility of cracking.
Before installing the fasteners, holes are drilled in the sheet, the diameter of which is not less than the diameter of the fastener rod. The minimum distance from the edge of the sheet is 60 mm, the installation step depends on the place of operation and the planned loads. It is better to drill with a victorious drill at medium or high speeds.
Flat slate is cut with a circular saw, angle grinder (grinder) with a diamond disc or a disc for concrete. When using a power tool, the process is fast, but there is a lot of dust, so you only need to work outside and wearing a respirator. To reduce dust, flat slate is moistened with water. If possible, put a wet rag on the intended cutting site in a few hours. You can just pour water and cut wet material, but this is more likely to ruin the same grinder or circular saw.