What are the blocks for building a house
The house should be comfortable, safe and warm. Everyone will probably agree with this. And it is also desirable to be inexpensive and to be built quickly. Oddly enough, there are such options. One of them is building blocks. It is not for nothing that there are more and more of them. But which blocks are best for building a house? Let's try to figure it out. First, determine your key positions and consider all materials based on them.
The content of the article
- 1 How to choose the best building material for your home
- 2 Block types
- 3 Lightweight concrete blocks for exterior and interior walls
- 4 Ceramic block or porous warm ceramic
- 5 Pressed cement blocks from sand concrete (besser-blocks)
How to choose the best building material for your home
In order for the built house to please you, you will have to choose the material for its construction yourself. Why? Because there is no perfect building block. They all have pros and cons. You just need to choose such an option so that the "minuses" are compensated or not so important, and the "pluses" are used in full. And the construction conditions are different. Some live in a rather warm climate, while others in the north. And yet everyone has their own "best" home. So even two neighbors can be built from different materials, but each of them will honestly believe that his version is better.
Usually people think of a house made of building blocks because it is faster than using traditional building materials. Speed is speed, but quality characteristics are equally important. And in order to choose them correctly, here's what you need to know.
- Ground water level. May be important if you are going to build a house with a basement or basement. You can, of course, make high-quality waterproofing of the foundation and a good drainage around the house and on the site, but this is a big investment of money and time. It is advisable to do drainage before the walls are erected, in parallel with the manufacture of the foundation.
- The type of foundation and the degree of its "stability". Some blocks do not tolerate movement, so you need to know how reliable and stable the base will be.
- How quickly the walls will need to be built.
- Will it be necessary to leave them for the winter or do you plan to immediately cover them with a roof. It depends on the timing and budget.
- Can you immediately do exterior decoration... Not all building block materials can easily tolerate wetting and must be immediately covered from rain, snow and frost.
- Do you want to have vapor-permeable walls or are thermal insulation and low heating costs more important?
As you can see, the list is long, but this information is necessary. Without them, it makes no sense to decide which blocks are best for building a house. You simply will not have criteria to choose from.
Block types
Block construction attracts with the fact that it takes little time to build. Much less than using the same brick. But what are the blocks for building a house, how they differ, what are their advantages and disadvantages. Here is a list of block materials for the construction of exterior and interior walls.
- Lightweight concrete blocks
- aerated concrete;
- foam concrete;
- polystyrene concrete;
- expanded clay blocks;
- cinder blocks
- Ceramic block or porous ceramics;
- Pressed cement-sand blocks (solid, hollow and heat blocks).
Next, we will consider the building blocks, their types and characteristics. We will also briefly describe the production process. In some cases, this helps to better understand the merits and demerits of the material.
Lightweight concrete blocks for exterior and interior walls
Lightweight concrete is of two types. One uses a lightweight aggregate that reduces the mass of the building stone or block. In the second, the weight is reduced due to porosity - the cement foams and solidifies in this state. In both cases, the mass of the building material becomes much lower, and the thermal and sound insulation characteristics are higher.
Aerated concrete blocks
Aerated concrete is a cement-sand mixture to which dry reagents are added to form foam. When water is added, the reagents react with the cement laitance, and active foaming begins. After increasing the volume, the solution is laid out in molds and waiting for ripening. As a result, aerated concrete consists of thin concrete shells, inside which air is trapped. That is, the block turns out to be light and warm, vapor-permeable. He is not afraid of water, but he “pulls” it solidly. So you need good waterproofing of the foundation and you should not tighten it up with finishing.
Advantages and disadvantages
With rather large dimensions (length 600 mm, height 200 mm, width - from 150 mm to 400 mm), the standard unit weighs a little. The exact weight depends on the brand, but the average density can be worked alone. For example, let's say that the mass of an M400 wall block with a thickness of 200 mm is about 13 kg, and a thickness of 250 mm is about 17 kg.
There are two technologies for the production of aerated concrete blocks. One by one, the solution is laid out in forms of a given size and then they are used. On the second, large blocks are made, and then they are sawn into smaller ones. The peculiarity of the second technology is that it allows you to maintain dimensions with high accuracy. This makes it possible to use not a masonry mortar made of cement and sand, but a special glue. It can be put in a very thin layer - just a couple of millimeters. What for? Yes, because the solution and the same glue have much worse thermal insulation characteristics than aerated concrete. And thin seams reduce heat loss. But the glue is expensive, so it adds to the building cost. But you can save on insulation.
Advantages of aerated concrete | Disadvantages of aerated concrete blocks |
---|---|
Precise geometry, which speeds up the laying and allows the use of a special adhesive in a very thin layer to improve the thermal properties of the wall. | The glue is expensive, it increases the cost of construction |
Easy to handle. Can be cut with a hacksaw | Reinforcement required to increase wall strength |
Steam conductive material | The outer finish must also be vapor permeable. |
Absorbs moisture, does not react well to freezing / defrosting (few cycles) | Good foundation waterproofing and exterior finishing required |
Large block | Does not tolerate bending loads, requires a stable, reliable foundation, not suitable for places with seismic activity |
Does not burn, does not support combustion | There may be problems hanging heavy objects on walls |
Made from environmentally friendly substances |
Aerated concrete is easy to process, it can be cut even with a hand saw or grooved with a metal strip. On the other hand, it is not so dense that you can hang heavy things on walls without special fasteners.
Of course, there were some drawbacks. Blocks are fragile, do not withstand bending loads.That is, it is better not to build a house from gas blocks on a pile or columnar foundation. Deep slab or tape only. The second point: in order for the walls to be stronger, steel reinforcement is laid in every third or fourth row. Door and window openings are also reinforced, an armored belt is made for the installation of a roofing structure. This significantly affects the cost of construction, and the cost of reinforcement must also be included in the estimate.
Types and varieties of gas blocks
Aerated concrete blocks are autoclaved and conventional hardening. For the construction of external walls, it is better to take an autoclaved one, since it has more stable characteristics. Such blocks are more expensive and they are better.
Aerated concrete can be not only made of cement and sand. Part of the cement is replaced with another binder. As a result, we get blocks from another lightweight aerated concrete:
- lime + cement - silicate concrete;
- crushed blast-furnace slag + cement - slag gas concrete;
- ash + cement + lime = zologazobeton.
Of all the listed blocks, silicate concrete blocks are used for the construction of permanent residences. They differ from ordinary aerated concrete in color. Aerated concrete is gray, silicate concrete is white. What does lime additive do? Decrease in price with a slight decrease in performance. But there is one rather significant disadvantage: lime corrodes steel. To keep the armored belts intact, they are placed in a DSP layer or polymer reinforcement is used.
Foam blocks for building a house
At first glance, foam blocks are very similar to aerated concrete. The difference is that ready-made foam is added to the mixture of concrete and sand, and not a dry reagent. The mixture is kneaded, placed in molds and left to dry. Actually, that's all. Very simple. This is the disadvantage. You can also make foam concrete in the garage. But we cannot speak of any stability of the parameters. And the material itself is not bad.
Advantages and disadvantages of foam concrete blocks
Thermal characteristics of foam concrete are among the best. Slightly worse than aerated concrete. Which means that the walls of foam concrete should be thicker. Is this good or bad? More wall thickness, more mass, more load on the foundation. This means an increase in the size of the foundation and the cost of it, although the material for the walls itself is cheaper. But there is no definite answer that it will be cheaper. You have to count.
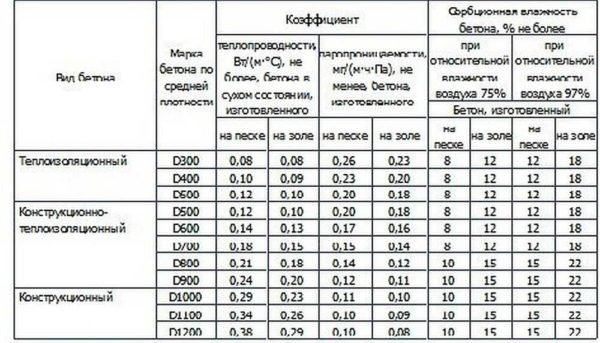
Foam concrete blocks for building a house are a good choice. Provided that they are made strictly according to technology
The worst thermal conductivity of aerated concrete is due to the fact that the walls of the air bubbles are thicker. That is, less air is contained in the same volume. This has two more "consequences" - higher material strength and greater weight. Higher strength is good. A self-tapping screw can already be screwed into the walls of foam blocks, and special fasteners generally hold "with a bang".
Pros of foam blocks for building a house | Cons of foam concrete blocks |
---|---|
Low density combined with high strength | Due to the simplicity of production, you can run into handicraft material with low quality |
Has good thermal insulation properties | Cannot withstand bending loads, requires a stable foundation |
Light weight, which means not too expensive foundation | Different pore sizes give heterogeneous characteristics |
The surface of the block is rough, which improves adhesion to plasters | Wider joint between blocks (up to 20 mm), which increases heat loss |
Vapor permeable wall | Requires a special approach to the choice of finishes |
Large block sizes speed up construction | |
Does not burn and does not support combustion | |
Environmentally friendly |
More weight is not so good anymore. This is again an increase in the dimensions of the foundation and the need to have an auxiliary for self-construction.Although when compared with the thickness of a brick wall, it is half the size. So the material is economical.
Another consequence of thicker cement walls is that it is more difficult to process. Not to compare, of course, with a brick, but not too easy.
The pluses of the material include its good soundproofing characteristics, incombustibility, and environmental safety. The material conducts steam, but not to the same extent as aerated concrete. But its frost resistance is higher. It absorbs moisture even better, so it also needs finishing.
In addition, foam concrete does not have such an ideal geometry. The size difference can be significant. This means that the masonry is carried out only for mortar and the seam is made thick enough to compensate for the difference in block sizes. Thick seams - a decrease in the thermal resistance of the wall as a whole.
To summarize, this is the picture we get. Inexpensive material, but you have to be sure of quality. The walls are erected quickly, the house turns out to be "quiet" and warm, the walls hold the screws. It is undesirable to leave without a roof for wintering. Finishing is needed, but not immediately after construction.
Polystyrene concrete blocks
Polystyrene concrete is a cement to which polystyrene granules are added, additives to improve workability. The mixture is mixed, water is added, poured into molds until solidification. With this technology, you don't have to wait for the ideal geometry, but the material is easily processed. You can cut with a hand saw. And this despite the fact that the strength and shape stability are high, the amount of shrinkage is minimal, and the mass is small (even less than that of aerated concrete of the same strength).
Polystyrene concrete blocks are rather large (15-30 per cubic meter), so construction is proceeding quickly. Placed on a regular solution, you can use glue. It comes in a thinner layer, although it costs more. A minus is typical for all lightweight concrete blocks - reinforcement is required to increase strength. Some manufacturers can lay rebar in the blocks themselves. These are used for laying load-bearing walls. Lintels are produced separately for installation above window and door openings. They definitely contain fittings inside. Due to its solidity, such a jumper works no worse than the corners, which are used as an alternative.
Advantages of blocks made of polystyrene concrete | Cons of polystyrene concrete building blocks |
---|---|
Lightweight, durable, tight | The technology is imperfect, the properties depend on the observance of the proportion and technology |
Easy to handle, large blocks, masonry is fast | Reinforcement is required, which is time-consuming and expensive |
Does not burn, does not support combustion | In the affected area crumbles |
Very good thermal conductivity and sound insulation characteristics | Requires special fasteners to secure something in the walls |
Good performance in frost resistance | Contains an artificial component |
Water vapor permeability on par with wood | Requires exterior finishing |
Low moisture absorption | |
Good sound insulation performance |
The vapor permeability of polystyrene concrete blocks is average. Flush with wood. The thermal conductivity is quite decent. For structural blocks with strength D400 - 0.15 -0.20 W / m ° C. Good indicators of frost resistance of the order of 50-70 cycles for the material of the same strength grade are good news. Compared to 20-25 foam concrete, this is already quite good.
Disadvantages and features
Minus - a house made of polystyrene concrete block requires cladding. Not for technical reasons, but for aesthetic reasons because of the unattractive appearance. What is good - it will easily survive a couple of winters without facing, as it has good frost resistance.What type of cladding? The best way out is a ventilated facade, but plaster is also possible. Only now the usual one does not hold well on cement. Required with special polymer additives and they are expensive. The good news is that the flow rate will be low - the wall is pretty flat. In addition, you can do without rough plaster. Fill in the mesh, and on it with decorative plaster. But how reliable this type of finish will be is difficult to say. They do it, but there are no reviews.
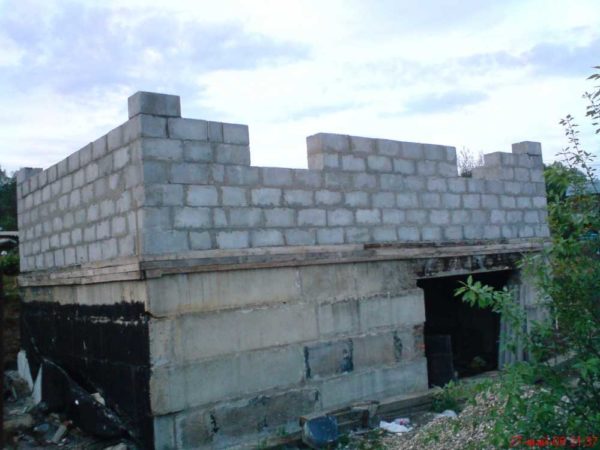
The size of a building block made of polystyrene concrete - length from 60 cm, width from 20 cm, height from 20 cm. Can be twice as thick / taller
As a summary. If you want to quickly and inexpensively build a warm house, then polystyrene blocks can be considered the best for building such a house. With one note - you have nothing against using polystyrene, and the need to think over the fastening to the walls does not bother you too much. After all, you will have to put windows and doors in some way.
Expanded clay blocks
Blocks from expanded clay concrete have been known for a long time. Expanded clay is added to the mixture of sand and cement, all this is mixed, then water is added. The technology for concrete is standard, but with its own characteristics. Expanded clay is fired clay and this type of material is hygroscopic. Therefore, more water is required to mix the solution.
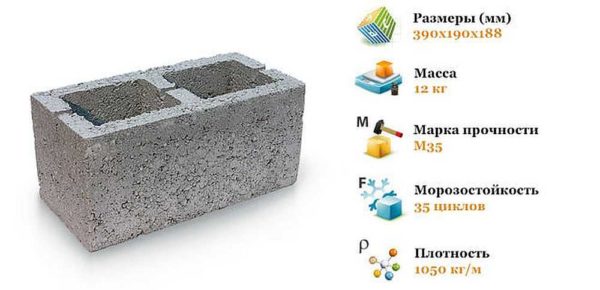
In the last century, block construction of houses was carried out mainly from expanded clay concrete blocks
In addition, expanded clay is not too well enveloped with a solution, so a longer batch is required. In production conditions, the problem of the required level of strength is solved in two ways: by autoclaving or vibrocompression. Without such processing, the material is obtained with lower strength characteristics. And since the technology is simple, then often "production" is opened in the garage, and the blocks are simply knocked out of the mold and dried. Moreover, like standard concrete, expanded clay concrete gains strength for 28 days. But it takes space to store it, so it can be sold sooner. If you know about it, you can put it at home for "ripening". If you do not know and immediately put it in the masonry, it may crumble. How to tell? Yes for the price. Factory ones are more expensive. But if you need blocks for building a house, then buying handicraft is dangerous.
Advantages and disadvantages
The advantages of lightweight aggregate concrete blocks are similar to those listed above: light weight, large size, good thermal insulation characteristics compared to brick. But solid expanded clay concrete has a lower thermal conductivity than all the materials described above. But it is much stronger. This allows you to make slotted blocks, and they are used for laying external walls. In this form, we obtain thermal insulation at about the same level. Plus, voids reduce weight, which is good.
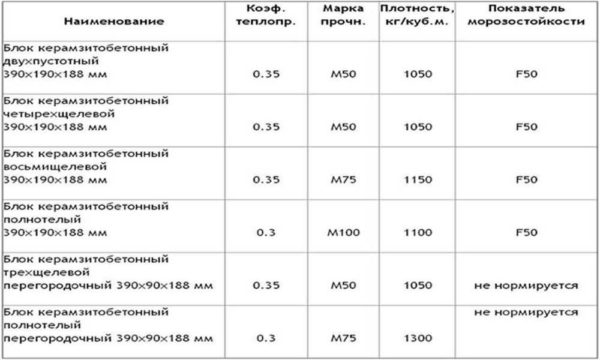
Blocks for construction from expanded clay concrete have average characteristics in terms of thermal efficiency
Other pluses. Walls made of expanded clay concrete do not require additional reinforcement, which allows laying the masonry faster. Blocks withstand bending loads better, so the requirements for foundations are less stringent. Buildings from expanded clay blocks can also be built on a pile or columnar foundation.
The disadvantages of blocks made of expanded clay concrete are quite serious. The first and the main one is that water absorption is high (on a level with aerated concrete), so external finishing is desirable immediately. Do not leave it without a roof for the winter, as moisture will pick up significantly and the service life will be reduced. There is no ideal geometry, but cement-based plasters lay very well and hold securely.
Advantages of expanded clay concrete blocks for building a house | Disadvantages of expanded clay concrete blocks |
---|---|
Simple technology, natural materials | There is a great chance to get on low-quality products |
High strength with low weight | Insufficient thermal insulation for the use of solid blocks |
Good thermal performance | Strongly absorbs moisture, needs exterior finishing and protection of interior walls from steam |
Medium frost resistance for vibropressed ones (about 35 cycles) and high for autoclave ones (up to 80 or 100 cycles) | Dimensional deviations |
Good adhesion to cement-based plaster | |
Does not burn and does not support combustion |
And yet, even if slotted blocks made of expanded clay concrete are used, additional external insulation is required for most of the territory. Due to its hygroscopicity, this material is not recommended for the construction of partitions in rooms with high humidity. That is, for the construction of a bath or partitions in the bathroom, it is better to look for another material. And in a private house, in order to avoid eternal dampness, a vapor barrier is laid from the inside. And in order to regulate the humidity in the room, good ventilation is needed.
What conclusions can be drawn? Earlier, before the appearance of aerated concrete, expanded clay concrete was considered the lightest and warmest material for building a house. Today it is clearly inferior in these indicators to foam-gas-polystyrene-concrete blocks and has solid disadvantages. Therefore, it is gradually being ousted from the market.
Cinder blocks
As the name implies, slag acts as a backfill in cinder concrete. In theory, blast furnace slag is used, which is formed during the smelting of ore and covers the metal. It has a porous structure and does not conduct heat well. That is why it was used to produce cheap blocks for housing. But in the days of the USSR, when materials were driven throughout the immense, one could hope that in regions where there are no steel-making industries, you would really get a cinder block. Today there is little hope for this - delivery is expensive, which makes the production of such material unprofitable.
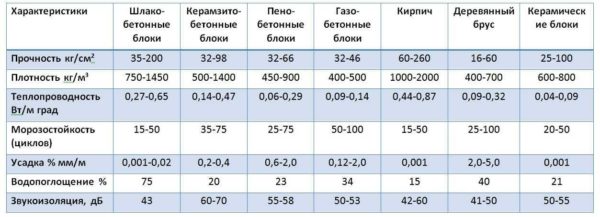
Comparison of lightweight concrete blocks using different technologies and with different aggregates
So what do we have? No slag in the cinder block. It is replaced with crushed stone, expanded clay, broken glass, brick fighting. That is, they also use "slag", in the sense of waste, but not blast furnace. As a result, the characteristics are unpredictable, the thermal conductivity is low, the durability is as lucky.
Even if we compare the characteristics of cinder blocks with blast-furnace slag aggregate, they are not impressive. And I must also add that its moisture absorption is very high - more than two times higher than that of foam and aerated concrete. And this is at a lower thermal conductivity in a dry state. So it becomes clear that this unit cannot be called the best, and it is far from the cheapest. Blast furnace slag costs a lot. This material is now clearly inferior in many respects. For the last twenty years he has been remembered "from old memory."
Ceramic block or porous warm ceramic
This porous ceramic block is produced using the same technology as bricks and from the same materials. The only difference is that the "body" of the material is not solid, but consists of voids and ceramic bridges. Such a structure is effective: for central Russia, a wall made of porous ceramics should be 50 cm. The same wall thickness is needed from aerated concrete. And additional insulation with this thickness is not required. That is, the wall will be single-layer, which is much better than multi-layer. And the finish can be made from facing bricks or clinker. Ceramics will make friends with ceramics without any problems. But not everything is so rosy.
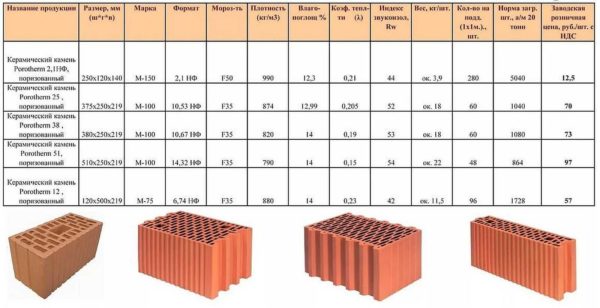
Hollow blocks for walls made of ceramics could be considered the best option, if not for a high percentage of battle and difficulty with fasteners
Advantages and disadvantages of ceramic blocks
The main advantages were listed - good thermal characteristics and low (compared to ordinary or even hollow brick) weight. But ceramics is fragile. And thin partitions break and break easily. When transporting, you can get about 10% of the battle. In addition, cutting off a ceramic block is not easy. The saw won't help here.Requires other, more serious equipment. Another drawback is that special fasteners are required, since only he can hold in thin walls.
Advantages of ceramic blocks | Cons of hollow ceramic blocks |
---|---|
Good thermal insulation performance | Fragile material that easily splits and breaks |
High level of sound insulation | Special tool required to cut blocks |
Average water absorption | Requires special fasteners |
Steam permeability | The blocks are not as big when compared to lightweight concrete |
Good frost resistance | Imperfect geometry, high cost for ground, which have stable dimensions |
High strength | |
The presence of a corrugated surface, which increases the thermal resistance of the masonry. | |
High heat absorption. It works like a large heat storage, but it is bad for building houses with periodic heating. |
Other advantages are the same as for bricks: natural ceramics, medium water absorption, frost resistance from 30 to 80 cycles, good sound insulation properties - up to 55 dB, which is a very good indicator. In addition, there is such a thing as heat capacity. It shows how much heat a material can accumulate in itself. The more heat it "takes" into itself, the longer it will give it back later. For houses with permanent residence, it is materials with a high heat capacity that are more comfortable. And for ceramics it is rather big. Such a wall is a kind of heat accumulator. For a home of permanent residence, this is good, but for a summer residence that is visited in winter only from time to time, it is bad. It takes a lot of fuel and time to warm up. So this building block is not the best for summer cottages or baths.
It should also be added that today the cost of a cube of a porous ceramic block and the cost of autoclaved aerated concrete are practically the same. In some places, aerated concrete is even more expensive. But the dimensions of aerated concrete blocks are larger, the consumption of glue and the time required are less. Time can be argued, since for ceramics the presence of armopoies is not necessary, but it will not be superfluous. And you can't argue with the size of the blocks. And with the precision of geometry. No, there are grinded ceramic blocks that can be customized. They can be installed with a minimum layer of adhesive. But such blocks are much more expensive. Nevertheless, taking into account all the facts, it is worth saying that we all know ceramics. So, all other things being equal, it is more reasonable to choose it.
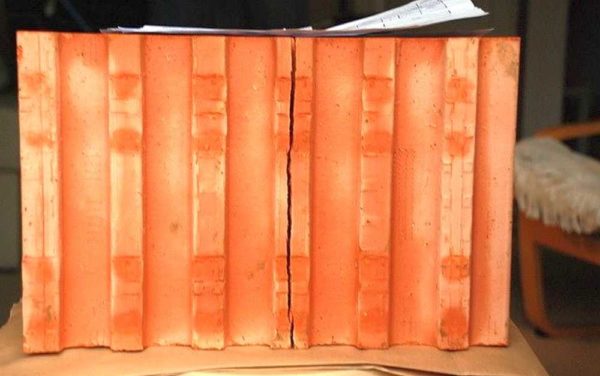
Lightweight blocks for construction made of porous ceramics have good characteristics, but they can be cracked, which do not contradict GOST. Some manufacturers change such material without problems. Others do not consider it a marriage.
Everything is true, but there is one setback. A ceramic block is a type of brick. And according to GOST, non-through cracks are allowed in the brick, if they do not affect the strength. Solid bricks do. The presence of small cracks on one of the sides is not considered a marriage and does not affect the quality of the masonry. But if there is a crack in one of the edges of the ceramic block, it will clearly not be as strong. Second. When one of the faces is torn, it diverges, the sides are no longer parallel. It is hardly worth using such a block in masonry, although technically this is not a marriage.
Pressed cement blocks from sand concrete (besser-blocks)
Another type of hollow building block is made from sand concrete. Full-bodied ones are made using the same technology, but they have low thermal efficiency. But the wall is practically a monolith, it is difficult to break through it, the bearing capacity is high. But such a house, in order to be warm, will have very thick walls, which will increase the cost of the foundation.
Therefore, a combined building is considered the best option. In the sense that the wall is laid from a solid and hollow vibropressed block. The outer layer is solid, the inner layer has voids. Thus, the strength of the wall and its bearing capacity are high, and the thermal performance is high.It should also be said that the technology allows one of the sides of the block to be made "face", with a smooth surface or under a "torn stone". Sand-cement vibrating blocks are good because you can add dye to them. Everything looks quite decent, and at the price such stones with a "front" side are only slightly more expensive. You just need special forms, and the technology does not change.
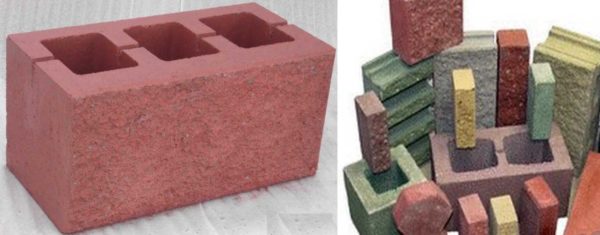
Which blocks are best for building a house? If strong walls are a priority, then vibropressed ones are out of competition
The process of forming vibropressed blocks is as follows: a mixture of cement and sand is diluted with water. The solution is poured into molds, which are then processed on a vibrocompression table. That is, the solution is simultaneously subjected to vibration and pressure. This gives it increased strength and allows you to make the walls thin, and the voids significant. All this makes it possible to reduce weight, as well as to increase the thermal performance. This technology has been used in America for a long time. Budget houses are built from such a building block. It is called the Besser-block.
Advantages and disadvantages of vibropressed blocks
The main advantage of this technology is vibration treatment with simultaneous pressure. The concrete stone is very durable and homogeneous. There are no voids, inhomogeneities, characteristics and properties are stable, the walls are even and smooth. And also such processing makes it possible to control the size. Of all the blocks that are poured into molds, this one has the best geometry.
Further by properties: high frost resistance - from 50 cycles (up to 300), strength - M100 or higher. The thermal conductivity of hollow blocks is 0.9 W / m², which is much lower than required, so either the wall must be thick, or it must be insulated. It absorbs moisture, but in small quantities, it is not afraid of getting wet. There is no data on the thermal conductivity of the solid block. You have to understand that they are extremely disappointing.
Reinforcement is recommended when building walls from hollow vibroblocks. Moreover, they do both vertical and horizontal. For vertical, rods are used, which would be good to connect with outlets from the foundation. And the horizontal reinforcement is a metal mesh. This is not a requirement, but stronger walls are obtained this way.
Of the "pure" disadvantages - a rather large weight and small size of the stone. This is when compared with lightweight concrete blocks. Accordingly, a foundation for a large weight needs a more powerful one, which leads to an increase in costs for it.
For the price - it is quite democratic, since the components are affordable, and the vibrating table is not such an expensive equipment as to greatly raise the cost. In general, quite a decent option. But no matter how you describe the merits, cement remains cement. And houses are rarely built from this material. But fences are often built or used as a facing stone. By the way, it is often called the “intake” block or Besser.
Heat block
The heat block is made on the basis of vibrocompression technology. This is a multi-layer structure, in the middle of which there is polystyrene, and on the sides there is a cement-sand vibropressed composition. Moreover, one side is front, painted in bulk and, as a rule, textured, and the other is a solid building stone that carries a load. To increase reliability, the structure is fastened with reinforcing rods.
That is, the heat block is a three-in-one material. Immediately, the wall is being built, and its thermal insulation and decoration. The idea is very interesting and tempting. But, as usual, the novelty raises concerns - how will such a cake behave over time? How reliable are such walls? In general, while people are in no hurry, although these blocks are better for quickly building a house.
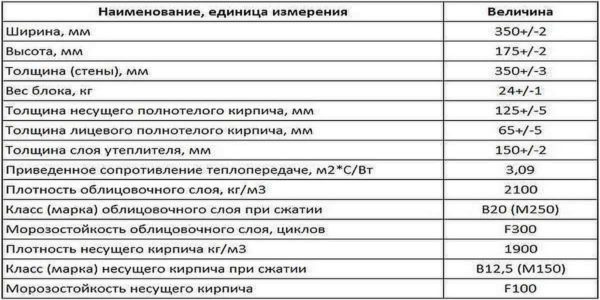
It is not so difficult to find characteristics here. Apparently, because thermal conductivity pleases
A village in the north of the Volgograd region, the temperature in winter can drop below minus 30. Mostly they are built from autoclaved aerated concrete, moreover, most of them put it on the edge, i.e. the wall thickness is 20 cm. At the same time, the house is warm. I have a summer kitchen and a sauna made of aerated concrete - everything is fine. Moreover, when I was building, they did not bring glue to our places, and masonry on cement. True, I deepened the seams from the inside and foamed them. Now, of course, everyone uses glue and the masonry does not freeze through the seam. The downside is that the material does not hold screws well - you need special fasteners for heavy objects.
I also saw a house made of non-autoclaved aerated concrete (gray) - an exception to the rule.
Expanded clay concrete is also rarely used.