Proportions of cement and sand for floor screed
Almost all modern floor coverings require a flat base, which is easiest to achieve with a floor screed. The process will take a long time. You will most likely have to wait about a month before laying the flooring, but the floor will be reliable. It is cheapest to make a screed solution from a mixture of sand and cement. There are other options though.
The content of the article
- 1 The composition of the mortar for the floor screed: DSP or concrete with gravel
- 2 Brand of cement-sand mortar for screed: choice of strength
- 3 The proportions of the classic DSP screed
- 4 Supplements: Needed or Not?
- 5 Calculation of the volume of the solution for the screed
- 6 Cement consumption for screed
The composition of the mortar for the floor screed: DSP or concrete with gravel
Floor screed is most often made from a cement-sand mixture. That is, the solution contains only cement and sand, sometimes with additional additives. In the classic version, the screed is poured only by mixing sand and cement in a certain proportion, the mixture is diluted with water. Such a solution is also called sand concrete. In the sense that only sand is used as a filler. This is the cheapest option, but not the only one.
With a screed thickness of more than 5 cm, concrete with fine gravel aggregate can be used. Classic concrete: a certain amount of crushed stone is added to the sand and cement. Its dimensions are no more than half the thickness of the screed. Since the minimum size of crushed stone is 20-25 mm, the minimum thickness of a concrete screed is emerging - 50 mm.
But concrete with gravel is heavier and more expensive. Its plus is that it is less susceptible to cracking during shrinkage and therefore it is poured with concrete warm floor... Few cracks are critical here. For a conventional leveling screed, shrinkage cracks are not such a problem. The budget, however, is usually limited and therefore the cement-sand mixture is more often chosen.
Sometimes gypsum-based compounds are used for screeds. But they are afraid of moisture, the solution has a shorter life, the surface strength is lower. All this makes them unpopular. Gypsum-based screed solution is a rarity in recent years.
Brand of cement-sand mortar for screed: choice of strength
What brand of cement-sand mortar is used for screed? Previously, they could put M50 or M75. Now the minimum is M150. Why? Because, above all, the requirements for finishing were much lower. What was previously considered normal - small pits, caverns, cracks - is now unacceptable. And this is not only "aesthetics". To a greater extent, these are the requirements of manufacturers of finishing coatings. They require an almost perfect surface that is not dusty, and this can only be obtained from a solution with a strength of at least M100.
There are other reasons why a higher grade is used. First. No one is sure about the quality of the cement, so they prefer to play it safe than redo it. Second, modern coatings require an even, solid foundation and the screed mortar must be strong. And thirdly, a low grade simply cannot be installed under self-leveling compounds or under modern tile adhesive with polymer additives. To prevent the two parts of the coating from delaminating, the difference in strength should be no more than 50 units. That is, if the leveling mixture has a strength of M250, the mortar for floor screed must be of strength M200 and not lower. It's the same with tile adhesive. So pay attention to this.
The proportions of the classic DSP screed
The classic mortar for floor screed, as already mentioned, is cement with sand, diluted with water. The proportion (amount of sand per unit of cement) depends on the required screed strength and the type of cement used. To make the floor surface strong, use expensive Portland cement grade M400 and above.
The cheaper M300 can also be used for screed floors in utility rooms. It will go a little more, but there will be savings. For the foundation in a house or apartment under modern coatings, it is better not to take such cement. The rework will require significantly more savings on cement.
For beginners in the construction business, it seems that if you take more cement, there will be a stronger screed. But no. The correct ratio of all components is important for strength, and an excessive amount of cement can lead to a decrease in strength. If you want a stronger screed, use high quality cement and measure the proportions accurately. By the way, you shouldn't take more water either. This will increase the fluidity of the mortar, but will increase the number of shrinkage cracks. So once again: to get strong and reliable concrete, you need to accurately observe the proportions.
What sand to take
It is better to take river sand, and it is washed, of at least two fractions: large and medium. Why river? Because it has sharp edges, and this reduces the likelihood that it settles into the lower layers. This is understandable. Why washed? There is a minimum of dust in it. The less dust, the higher the strength of the mortar. The sand also needs different sizes for the mortar strength to be normal.
If you are going to lay an expensive coating on the floor with high requirements for the strength of the base (parquet, parquet or engineered board, vinyl tiles), it is better to take just such sand. There will be fewer problems.
Kneading sequence
When making a floor screed solution, first mix the dry components - cement and sand. With manual kneading (in a trough), there is not much difference between what to throw in first - cement or sand. If using concrete mixer, immediately throw sand and twist it for a couple of minutes without cement. Then, gradually, cement is usually added with shovels. After each portion, they wait until it is more or less evenly distributed, then throw in the next one. After adding all the binder, mix until you get an evenly colored mixture.
When the dry components are mixed until a uniform gray mass is obtained, water is gradually introduced. It is counted from the amount of cement. Usually, 0.45-0.55 parts of water are taken for 1 part of cement. Why don't they indicate exactly? Because the amount of water depends on the moisture content of the sand. And it is advisable to pour a minimum of water: this way there will be less cracks when drying.
Ready mortar or sand-cement mixture
Those who have at least once independently kneaded DSP or concrete are more likely to buy ready-made concrete. And not a mixture of sand and cement in bags, but concrete from a concrete mixer. Yes, it is more expensive for the money, but much less time and effort is required. Another plus of this solution: pouring without cold seams. This means fewer cracks and problems in the future. The next plus is that concrete mixers can deliver the solution to the desired floor. Imagine that you have to drag and drop a couple of tons of sand and cement. Even if there is a freight elevator, it is not easy. It can be costly if you pay the helpers. Climbing stairs "on your shoulders" is generally a problem.
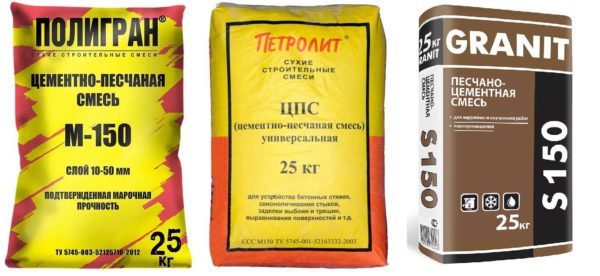
So that you do not care about the proportions of cement and sand, you can buy a ready-made mixture in bags
What are the advantages of buying ready-made sand-cement mixture in bags? In that the proportion is kept exactly, the sand is used in several fractions and in the right quantities. That is, the screed is guaranteed to have the required strength. The downside is the price.You can buy the same amount of cement and sand for a much lower amount. This is if you do not bother with the fractions of sand. If you take care of this too, then the savings will become less: not all factions are cheap.
Supplements: Needed or Not?
In a classic floor screed solution, it may be recommended to add plasticizers and fiber or other substances for micro-reinforcement. Are they needed or not? First you need to understand what it is and why.
Plasticizing additives
Plasticizers are substances that increase the plasticity of DSP. It is easier to work with such solutions. Concrete with plasticizer adheres better, smoothes easier, gives a smoother surface. In general, if all the components of normal quality are well mixed, then it is not difficult to work with mixed water with them. With additives, of course, it's easier. But factory-made plasticizers cost a lot of money, and this increases the cost of the screed. They need to be added in small quantities, but the bill when pouring the floor in the house goes to cubic meters, so the costs will be tangible.
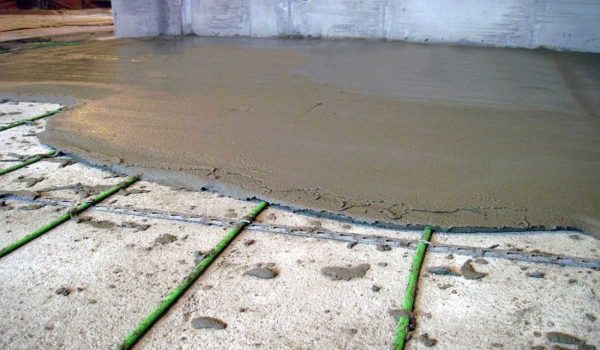
When mixing, the proportions of the solution must be observed with great accuracy. To make the solution fit better, plasticizers are added, and not more water
As usual, the craftsmen have found a substitute for factory-made plasticizers. Ordinary soap is added to the solution. Its consumption is very small - a glass or so for one concrete mixer. The plasticity of the solution increases, so many people use this type of additive. For beginners, it is worth saying: do not exceed the recommended dose. The solution will not get better, but it may well be worse. Soap increases plasticity by "lubricating" the sand, reducing its "adhesion" to the cement slurry. Excessive dosage may lead to a decrease in the strength of the screed So be specific.
Micro-reinforcement
As you know, when dry, the cement-sand mortar shrinks. The amount of shrinkage is from 1.5% to 3% by volume. Specifically, the percentage of shrinkage depends on the amount of impurities (if the sand is washed, the shrinkage will be less), the correctly selected composition of the aggregate (in this case, sand), the exact proportions and a number of conditions and factors.
Everything would be fine, but cracks form in the solution when it shrinks. They are always there, only larger or smaller, more or less. To reduce the number of cracks, micro-reinforcement materials are added to the solution. Fiber is most often used in everyday life. It happens:
- fiberglass;
- basalt;
- metal;
- polypropylene.
The most popular for domestic purposes is polypropylene fiber. It is the most inexpensive and gives a good result. How does it work? 100 grams of this supplement contains a huge amount of synthetic fibers. They are very thin, but synthetics are highly durable. These fibers are randomly but evenly distributed throughout the thickness of the solution. In concrete, they form a kind of lattice in space. When stresses arise when the screed dries, they bind the parts of the solution together, reducing the number and size of cracks.
The second effect of fiberglass is a smoother and more durable surface. So this screed additive is more useful and definitely worth using. But again, strictly according to the recommendations. It seems that if you add more fiber, there will be fewer cracks, but no. The strength of the screed will decrease.
Calculation of the volume of the solution for the screed
To determine the volume of materials, you need to know how much solution is required. Then, using the required proportions for the screed, it will be possible to calculate the approximate amount of sand and cement. To calculate the solution, you need to know the area over which we will pour the solution and the layer thickness.
Calculate fill area simple: the length of the room in meters is multiplied by its width. We get the area. You should already know the maximum and minimum screed layers.By the degree of evenness of the base, you can determine the approximate average thickness. If the found area is multiplied by the thickness of the screed and we get the required volume of the solution.
Let's take an example. The room is 2.8 m by 3.4 m, the screed thickness is 6 cm. We find the pouring area - 2.8 * 3.4 = 9.52 m². To get the cubic meters of concrete that we need, we need to convert 6 cm to meters. To do this, divide 6 cm by 100. We get 0.06 m. Now we multiply the pouring area by this figure: 9.52 * 0.06 = 0.5712 m3. That is, for a room area of 9.5 squares with a screed thickness of 6 cm, approximately 0.6 cubic meters of mortar will be required. With such a volume, you will definitely have to mix the floor screed solution yourself. No concrete plant will deliver less than a cubic meter of mortar.
If it will be necessary to pour the screed in several rooms at once, you can first calculate the area of all rooms for pouring, then multiply by the thickness of the screed. This option is possible if there are no large differences in height between different rooms. If in one room the screed is 6 cm, in another 9 cm, it is better to count the volume for each room separately, and then add the results.
Cement consumption for screed
If you decide to mix the screed solution yourself, you need to decide on the amount of cement that you need. It can be calculated based on the found solution volume. There are tables that show the consumption of cement for the screed, depending on the brand of solution and binder.
Let's calculate the amount of cement for one cube of sand concrete screed M150. If we use M400 cement, 400 kilograms of cement will be consumed per cube (according to the table). To find how much cement will be needed for the example described above, it is necessary to multiply the found volume of the solution by the norm: 0.6 m³ * 400 kg = 240 kg. That is, this room will need 240 kilograms of cement. To determine the number of bags, divide this figure by the weight of the cement in the bag.
- If there is 50 kg of cement in a bag, you will need: 240 kg / 50 kg = 4.8 bags.
- When packaged in 25 kg: 240 kg / 25 kg = 9.6 bags.
Other packaging also happens, but is rare. When you decide on the brand and manufacturer, you can accurately calculate the number of bags of cement for the floor screed.
Even cement consumption can be calculated based on the amount of sand available. You never know. Maybe someone will buy sand and so that there is no residue left, it must be used up all.
Blah, what are you smoking there? “It's better to take river sand. Why river? Because it has sharp edges. " Where do you get the sharp edges from? All the water grinds off, and it turns out like pebbles, smooth. Career washed, and you will be happy. For the same reason, there should be crushed stone, not gravel.