Diy waste oil oven
It is always pleasant to use waste materials with benefit. And if it concerns fuel and heating, it is also very profitable. Waste oil heating stoves are a prime example. They can use any oil that can burn. Transmission, diesel, machine, confectionery, vegetable ... Really any. There are no problems with fuel for such units. What they found, they filled it up. Moreover, a do-it-yourself oven is also made from waste materials: an old gas or oxygen cylinder, pipe sections of different diameters or pieces of metal.
The content of the article
How homemade ovens work
If any waste oil is simply set on fire, it will smelt mercilessly and "smell" even more actively. Therefore, direct combustion is not used. First, volatile substances evaporate, then they are burned. This is the basic design principle. Therefore, in some versions, the furnace has two combustion chambers connected by a tube in which holes are made.
The fuel is heated and evaporated in the lower chamber. Combustible vapors rise upward. Passing through a pipe with holes, they mix with oxygen dissolved in the air. Already in the upper part of this pipe, the mixture ignites and burns out in the second chamber. Moreover, the combustion of vapors occurs with the release of much more heat and less smoke. With the right technology, there is practically no smoke, as well as soot.
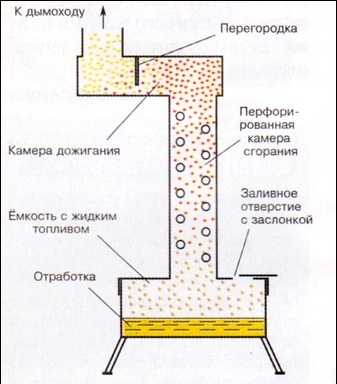
Waste oil furnace with air supply pipe
The second method of dividing "heavy" fuel (oil of any origin) into "flammable" components is more efficient, but also more difficult to implement. For efficient evaporation, a metal bowl is installed in the lower chamber. It heats up, drops of working off falling on it instantly turn into volatile combustible vapors. In this case, the glow turns out (with the correct mode) white-blue, as when burning a plasma. Hence another name for this design came from - with a plasma bowl.
To achieve the best fuel combustion efficiency, the used oil must be supplied to the lower chamber in very small portions. In some versions - in drops, sometimes in a thin stream. That is why this technology is called drop feeding.
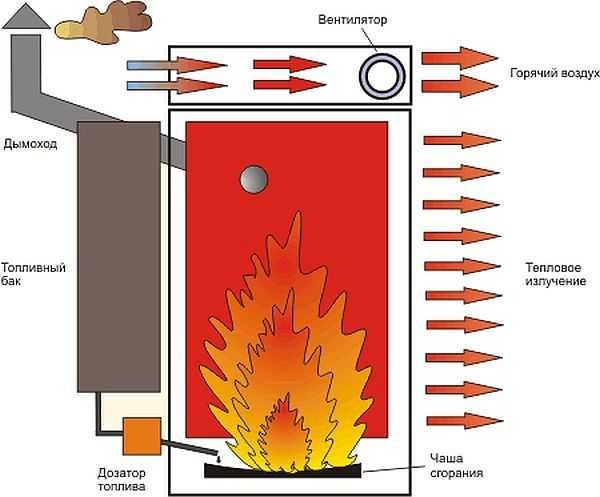
Principle of operation of a waste oil furnace with a plasma bowl
These are the basic principles of the "operation" of home-made heating units. There are a very large number of combinations and variations. Several of them are described below.
You can see an example of the combustion of a working out in a plasma bowl in the video below. This is a Gecko mining furnace, it has a built-in water heater and can work as a heating boiler.
Advantages and disadvantages
The main and main advantage is that it uses spent fuel and oils, which were otherwise subject to disposal. With the observance of technology, the combustion is so complete that practically no harmful emissions into the atmosphere occur. The rest of the pluses are no less significant:
- simple construction;
- high efficiency;
- low cost of equipment and fuel;
- works on any oils, organic, synthetic, vegetable origin;
- content of up to 10% of pollutants is allowed.
There are also serious disadvantages. And the main thing is that if the technology is not observed, the combustion of fuel does not occur completely. And his vapors get into the room, and this is very dangerous.Therefore, the main and main requirement: furnaces operating on waste oil are installed exclusively in rooms with a ventilation system.
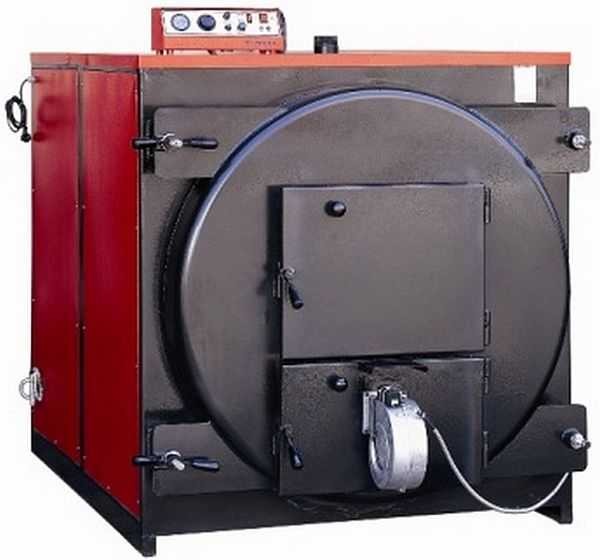
For comparison: this is a waste oil boiler with an inflatable burner. The technology is different, as is the design (more in the video almost at the end of the article)
There are also disadvantages:
- to ensure good draft, the chimney must be straight and high - at least 5 meters;
- requires regular cleaning of the bowl and chimney - daily;
- problem ignition: you first need to heat the bowl, then supply fuel;
- water-heating options are possible, but their independent design is a difficult task - the temperature in the combustion zone cannot be greatly reduced, otherwise the whole process will fall apart (as an option, install a water jacket on the chimney, here it certainly will not interfere with the decomposition of the fuel).
Because of these features, such units are rarely used for heating residential buildings. If they are put on, then in separate rooms and in a modified form.
Application area
In the basic version, a homemade waste oil stove heats the air. They are also called heat guns, heat generators or air heaters. For heating living quarters in this form, it is rarely used: the air is overdried, oxygen from the hot metal walls is burned out. But in order to maintain normal temperature in industrial or technical premises, such units are very effective: they quickly raise the temperature. They can be seen at service stations, car washes, in garages, production workshops where there are no combustible materials, in warehouses, in greenhouses, etc.
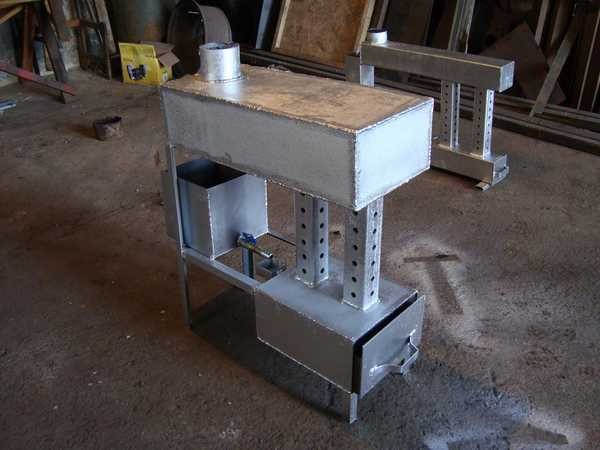
Do-it-yourself ovens - for a garage, the best option
Many options can be modified: they can be equipped with a coil for heating water or made a water jacket. Such equipment already belongs to the category of hot water and can be installed in a hot water heating system. Without automation, a working furnace with a water circuit requires constant monitoring, but for summer cottages, household buildings with livestock, etc. this is a great option.
How to make a waste oil oven
Today there are already more than a dozen different designs. They use different methods of extracting heat energy, they have different structures.
Furnaces for incineration of waste from a pipe
It is easier to make the oven if the body is already ready. As such, you can use a gas or oxygen cylinder, a thick-walled barrel or pipe. The diagram below explains how to make a waste oil stove from a pipe.
The operation of this unit is based on evaporation in a plasma bowl. It can produce up to 15 kW of heat (on average, it can heat 150 square meters). Greater heat transfer due to any changes (the size of the furnace or an increase in air supply) is impossible: the thermal regime will be violated and instead of a larger amount of heat, a greater amount of fumes will be obtained, and this is unsafe.
The assembly order is as follows:
- We make the case.
- We take a thick-walled pipe with a diameter of 210 mm, a wall thickness of 10 mm. Height 780 mm.
- Cut out a bottom with a diameter of 219 mm from sheet steel with a thickness of at least 5 mm and weld it on one side. This is the bottom.
- Legs are welded to the bottom (they can be made from bolts).
- A viewing window is made at a distance of 70 mm from the bottom. Through it, it will be possible to monitor the combustion and warm up the bowl at the "start". Dimensions, respectively, make it convenient for you. The door itself is made from a cut out piece of pipe by welding a thin shoulder. But everything should be closed tightly, therefore an asbestos cord is laid around the perimeter of the door. You can use furnace casting, then the dimensions of the hole are cut out for it. You can fasten it with bolts directly to the body (an asbestos cord is required here).
- On the opposite side of the body, departing 7-10 cm from the top, a pipe is welded to remove flue gases. Its diameter is 108 mm, wall thickness is 4 mm.
- Making a cover.
- A circle with a diameter of 228 mm is cut out of metal 5 mm thick.
- A collar of a strip of metal 40 mm wide is welded along the edge, the thickness of the metal is 3 mm.
- A hole with a diameter of 89 mm is cut in the center of the lid, the second with a diameter of 18 mm is cut out from the side. The smaller hole serves as another viewing window; a cover is made for it, which is also used as a safety valve.
- We make a pipe for supplying air and fuel.
- We take a piece of pipe 89 mm in diameter, with a wall thickness of 3 mm, and a length of 760 mm.
- Departing from the edge of 50 mm, 9 holes of 5 mm in diameter are drilled around the circumference.
- 50 mm above these holes, two more rows of holes with a diameter of 4.2 mm are made, 8 pieces in each row.
- Having risen even higher by 50 mm, make a fourth row of holes 3 mm in diameter. There should be 9 of them.
- On the same side, along the edge of the grinder, cuts are cut with a thickness of 1.6 mm and a height of 30 mm. They need to be made 9 pieces around the circumference of the pipe.
- From the other end of the pipe, stepping back 5-7 mm, cut a hole with a diameter of 10 mm.
- Insert the fuel supply pipe into the cut hole. Its diameter is 10 mm, wall thickness is 1 mm. It ends on the same level with the air supply pipe. The length and angle of bend depend on where the container with fuel will be located.
An example of a homemade stove from a pipe
- The finished air and fuel supply pipe is welded to the cover. It is set so that it does not reach the bottom of the case by 120 mm.
- We make a bowl for fuel
- Now a piece of 30 mm is cut from a pipe with a diameter of 133 mm, with a wall thickness of 4 mm.
- Cut out a circle with a diameter of 219 mm from 2 mm thick sheet steel.
- We weld to a piece of pipe. The result is a bowl where fuel is supplied.
- Assembly.
- A bowl is installed inside the body at a distance of 70 mm from the bottom. It can be watched (and ignited) from the lower inspection hatch.
- Install the cover with the fuel / air supply device.
- A chimney is installed on the chimney. Pipe with a diameter of 114 mm, a wall of 4 mm. Its height is at least 4 meters. The part that remains in the room may not be isolated; it is better to insulate it on the street. Chimney - only vertically upwards, inclined sections are excluded.
After installing the oil tank, testing can begin. First, a little paper is placed in the bowl, a flammable liquid is poured, everything is set on fire. After the paper is almost burnt out, the oil supply opens.
It is not for nothing that this drawing of a waste oil furnace is given with such an accurate indication of materials. You need to use just such parts. As a result of the work of a home-made stove, at a consumption of 1-1.5 liters of fuel per hour, you can heat the room up to 150 "squares".
Drawing of a furnace from a pipe or cylinder in video format
The furnace on waste oil from a cylinder (oxygen or gas) is presented by the author in the video. The design is similar to the one described above, but with original modifications (and it is a little simpler)
DIY mini oven for working off
This home-made stove, with its small size and weight (10 kg), fuel consumption of about 0.5 lira per hour, produces 5-6 kW of heat. You can melt it harder, but you don't need to: it can explode. The design is loved by motorists: the garage heats up quickly even in extreme cold, oil is consumed sparingly, and even compact. Therefore, it can be called "garage".
The fuel tank of this small air cannon is assembled from the bottom and top of a standard 50 liter gas cylinder. It turns out a very reliable design (save at least one circular seam from the cylinder - there is an O-ring, which will give greater strength. You can make a tank from any other container of similar dimensions: 200-400 mm in diameter and about 350 mm in height.
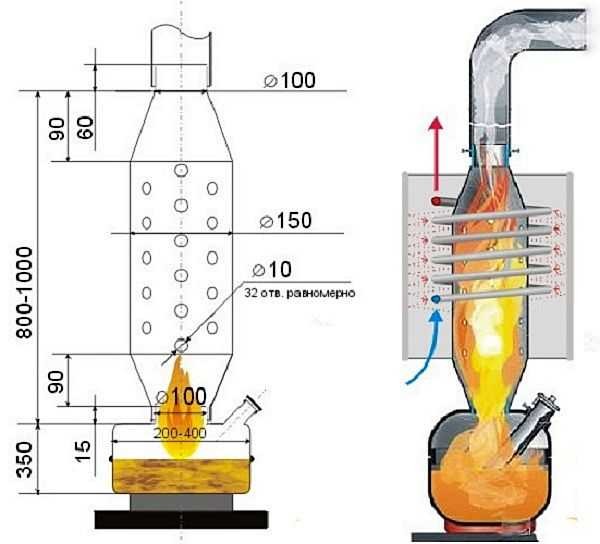
A small furnace for testing, it weighs about 10 kg, it is easy to make it with your own hands
In addition to the fuel tank, you need to make a pipe in which the fuel-air mixture is mixed. The wall thickness is at least 4 mm. You can use a pipe of a suitable diameter. The cones are welded from structural steel not thinner than 4 mm.
The dimensions of the waste oil furnace indicated in the drawing can be adjusted up or down, but only by 20 mm - no more. Especially carefully it is necessary to boil the seams in the places of the funnels: here the fuel-air mixture lingers for a long time, which is why the temperature is considerable.
The length of the chimney pipe is no more than 3.5 meters. Otherwise, due to too good traction, the fuel will be drawn into the pipe, which will significantly increase consumption and reduce heat transfer.
The picture on the right shows a hot water version of a homemade stove. Around the upper part of the afterburning zone, several turns of a steel tube are made, through which water is passed. To prevent the temperature of the gases from dropping too much, the coil is closed with a heat-reflecting steel casing. Cold water is supplied from below, passing in a spiral, heats up and goes into the system.
Miracle oven for testing
This option is very popular with summer residents and garages. Convenient small stove that is made with round or square burning zones. The design is so successful that there are even industrial options. For example, one of the companies sells it under the name Ritsa. The diagram shows all the required dimensions.
A video report on how to assemble this oven will help you navigate the order of work.
The video below shows an option with square containers, its filling and dimensions.
Factory options
Stoves operating on waste oil are made not only by the artisanal method, they are also produced by industry. Moreover, there are both imported and Russian. But the type of construction they have is different.
European or American mining boilers belong to the category of liquid fuel furnaces. They use the principle of pressurization: oil is sprayed into small droplets, combined with an air stream. And already the fuel-air mixture is ignited. Imported factory furnaces use the same principle, only a special burner is installed in which the fuel is heated before spraying.
To appreciate the difference in technology and structure, watch the following video. The device is completely different.
In most Russian-made stoves, the first principle is used - there is a hot (plasma) bowl in which liquid fuel is converted into gaseous fuel, mixed with air and burned. The following units are built on this principle:
- Gecko. Produced in Vladivostok. They make units with a capacity of 15, 30, 50 and 100 kW / h. These are hot water boilers that are built into the hot water heating system. Prices from 70,000 rubles for a 15 kW boiler.
Boilers on the development of Russian production "Gecko"
- Typhoon. They are produced by the company "Belamos". These are heat generators: they heat the air. There are two options - Typhoon TM 15 and TGM 300, they produce 20-30 kW / h (price: 45,000 rubles and 65,000 rubles, respectively).
- Herringbone-Turbo, there is 15 kW, there is 30 kW. These installations heat the air, but it is possible to make a water jacket.
- Furnaces "Teplamos" with a capacity of 5 kW / hour to 50 kW / hour. Belong to the category of heat guns (heat the air). Work begins with the electric heating of the plasma bowl, when the required temperature is reached, the fuel supply starts and the forced air supply to the combustion zone is switched on. The price of these units is from 30,000 rubles for a 5-15 kW unit.
Drawings and diagrams
There are many furnace models that use waste oil. And below are several schemes that can give you an idea, and a do-it-yourself oven will be efficient, economical and safe.
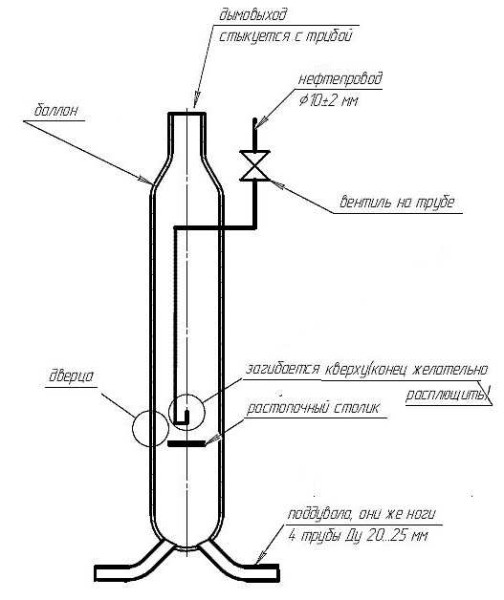
Oxygen cylinder furnace
Hello. I made a furnace as in the drawing "Mini furnace for working off with my own hands", but since the power of 2-3 kW is enough for me, I reduced the dimensions by 50 mm. combustion pipe 100 mm. and tapering at the top and bottom up to 70 mm. The opening for the filling and the control damper is 50 mm. The number of openings in the combustion pipe is 30 pcs. 8 mm each. Oil container with a diameter of 400 mm. and a height of 150 mm .. When firing up, when the oil starts to warm up, the stove starts to puff and goes out. (((Advise what needs to be done to correct the situation. Yes, the chimney is 2 meters.
It turns out that there is not enough oxygen for combustion?
1. Weld a short pipe to the burner (20-50 mm) so that the oil evaporates less intensely.
2. Or close the holes on the bottom of the burner and drill new ones higher up.
I would try these options. In general, to reduce the power, it is necessary to reduce the rate of oil evaporation, for example, the diameter of the tank must be reduced or it must not be allowed to overheat in other ways.