Soldering wires with a soldering iron: how to do it right
One of the most reliable ways to connect wires is soldering. This is a process in which the space between two conductors is filled with molten solder. In this case, the melting point of the solder should be lower than the melting temperature of the metals to be joined. At home, soldering is most often used with a soldering iron - a small device powered by electricity. For normal operation, the power of the soldering iron must be at least 80-100 watts.
The content of the article
What you need for soldering with a soldering iron
In addition to the soldering iron itself, you will need solders, rosin or fluxes, it is desirable to have a stand. Even in the process, you may need a small file and small pliers.
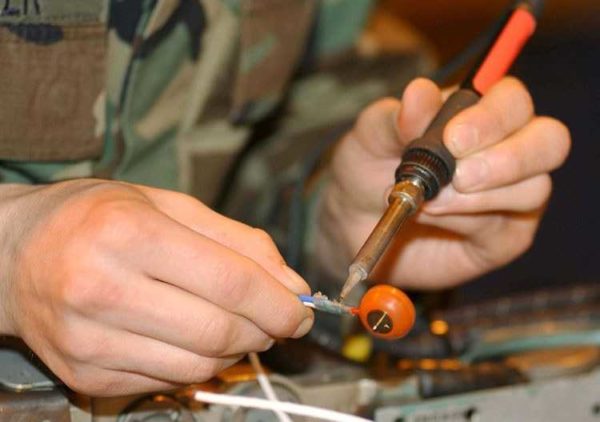
Most often, you have to solder copper wires, for example, on headphones, when repairing household appliances, etc.
Rosin and fluxes
To get a good connection of the wires, it is necessary to clean them from dirt, including from the oxide film. If the mono-cores can still be cleaned by hand, the stranded conductors cannot be cleaned normally. They are usually treated with rosin or flux - active substances that dissolve contaminants, including an oxide film.
Both rosin and fluxes work well, only it is easier to use fluxes - you can dip the brush into the solution and quickly process the wires. Put a conductor in the rosin, then heat it up with a soldering iron so that the molten substance envelops the entire surface of the metal. The disadvantage of using fluxes is that if they remain on the wires (and they remain), they gradually corrode the adjacent sheath. To prevent this from happening, all soldering points must be processed - wash off the remnants of the flux with alcohol.
Rosin is considered a versatile product, and fluxes can be selected depending on the metal that you intend to solder. In the case of wires, this is copper or aluminum. For copper and aluminum wires, they take flux LTI-120 or borax. A homemade flux made from rosin and denatured alcohol (1 to 5) works very well, in addition, it is easy to do it yourself. Add rosin to alcohol (preferably dust or very small pieces of it) and shake until dissolved. Then this compound can be used to process conductors and strands before soldering.
Solders for soldering copper wires with a soldering iron use POS 60, POS 50 or POS 40 - tin-lead. For aluminum, zinc-based compounds are more suitable. The most common are TsO-12 and P250A (made of tin and zinc), grade A (zinc and tin with the addition of copper), TsA-15 (zinc with aluminum).
It is very convenient to use solders containing rosin (POS 61). In this case, there is no need for preliminary processing of each conductor in rosin separately. But for high-quality soldering, a soldering iron must be powerful - 80-100 W, which can quickly heat up the soldering point to the required temperatures.
Supporting materials
In order to normally solder the wires with a soldering iron, you also need:
- Stand. It can be made of metal completely or on a wooden / plastic stand fixed metal holders for a soldering iron. It is also convenient if you have a small metal rosin box.
- File. Before work, the soldering iron is sharpened. It should be smooth and clean without any carbon deposits. Then it is easily soldered.
- Pliers.It is difficult to hold wires with your fingers during soldering - copper and aluminum have high thermal conductivity, which leads to rapid heating of nearby areas. Therefore, it is more convenient to solder the wires with a soldering iron if you hold them with pliers. Only the tool should be miniature, with thin handles and jaws. In principle, you can use tweezers, but it is advisable to put a heat shrink tube on the top of it (where you hold your fingers) - the steel also heats up quickly.
Alcohol may be required to remove the flux, and electrical tape or heat shrink tubing of various diameters for insulation. That's all the materials and tools without which soldering wires with a soldering iron is impossible.
Soldering process with an electric soldering iron
The entire technology of soldering wires with a soldering iron can be divided into several successive stages. All of them are repeated in a certain sequence:
- Preparation of conductors. When soldering wires, they are freed from insulation. After that, the oxide film is mechanically removed from them. You can use a small piece of fine-grain sandpaper. The metal should shine and be light.
- Tinning. The soldering iron is heated to the melting point of the rosin (when touched, it begins to actively melt). Take a conductor, bring it to a piece of rosin, heat it up with a soldering iron so that the entire stripped part of the wire is immersed in rosin. Then a drop of solder is taken on the tip of the soldering iron and spread over the processed part of the conductor. The solder spreads quickly, covering the wire with a thin layer. To distribute it faster and more evenly, turn the wire slightly. After tinning, copper conductors lose their redness and become silvery. This is how they process all the wires that will need to be soldered.
- Tinned conductors are folded together, straightening them with your fingers so that they fit snugly against one another. If the soldering needs to be long, twisting can be done. Holding the conductors, they take solder on the tip, press it to the soldering point, applying some effort. In this case, the soldering site heats up, the rosin begins to boil, the solder spreads. When it covers the entire zone, flows between the conductors, we can assume that the soldering of the conductors with a soldering iron is over. They are kept motionless for some time - until the solder cools down (to speed up the process, they blow on this place).
That's all, actually. In the same way, you can solder two or more wires, you can solder a wire to some kind of contact pad (for example, when soldering headphones - you can solder the wire to the plug or to the pad on the headphone), etc.
After you have finished soldering the wires with a soldering iron and they have cooled down, the connection must be insulated. You can wrap up electrical tape, you can put on, and then heat up the heat shrink tube. When it comes to electrical wiring, it is usually advised to first wrap a few turns of electrical tape, and put on a heat-shrinkable tube on top, which to warm up.
Differences in technology when using flux
If an active flux is used instead of rosin, the tinning process changes. The cleaned conductor is lubricated with the compound, after which it is warmed up with a soldering iron with a small amount of solder. Then everything is as described.
There are differences when soldering twists with flux. In this case, you can not tin each wire, but twist it, then treat it with flux and immediately begin to solder. The conductors do not even need to be cleaned - active compounds corrode the oxide film. But instead of this, you will have to wipe the soldering points with alcohol - in order to wash off the remnants of chemically aggressive substances.
Features of soldering stranded wires
The soldering technology described above is suitable for single conductors. If the wire is stranded, there are nuances: before tinning, the wiring is untwisted so that everything can be dipped in rosin.When applying solder, make sure that each wire is covered with a thin layer of solder. After cooling, the wires are twisted again into one bundle, then you can solder with a soldering iron as described above - dipping the tip into the solder, warming up the soldering point and applying tin.
Is it possible to solder copper wire with aluminum
The connection of aluminum with other reactive metals cannot be done directly. Since copper is a reactive material, copper and aluminum are not bonded or soldered. The point is too different thermal conductivity and different conductivity. With the passage of current, aluminum heats up more and expands more. Copper heats up and expands much less. Constant expansion / contraction to varying degrees leads to the fact that even the best contact is broken, a non-conductive film is formed, everything stops working. Therefore, copper and aluminum are not soldered.
If there is such a need to connect copper and aluminum conductors, a bolted connection is made. Take a bolt with a suitable nut and three washers. At the ends of the wires to be connected, rings are formed to fit the bolt. Take a bolt, put on one washer, then a conductor, another washer - the next conductor, on top - a third washer and fix everything with a nut.
There are several other ways to connect aluminum and copper lines, but soldering does not apply to them. You can read about other methods here, but bolted - the most simple and reliable.