Dikişler nasıl doğru pişirilir: dikey, yatay, tavan
Elektrik kaynağında, metali ısıtmak için bir elektrik arkı kullanılır. Parça ve elektrot arasında oluşur - iletken metalden (bazen metal olmayan) bir çubuk. Metal, ark sıcaklığından erir. Parçaların birleşim yerindeki füzyon bölgesine kaynak (kaynak) dikişi denir. Farklı metaller ve farklı bağlantı türleri için kaynak tekniği, elektrotun konumu, hareketinin hızı ve genliği değişebilir. Bağlantı sadece güvenilir değil, aynı zamanda güzel olacak şekilde bir dikişin nasıl düzgün şekilde kaynaklanacağı, daha fazla konuşalım.
Makalenin içeriği
Kaynak türleri ve ek yerleri
Dikişler oldukça kapsamlı bir sınıflandırmaya sahiptir. Her şeyden önce, yapanların sendika türüne göre ayrılırlar. Güvenilirlik gereksinimlerine bağlı olarak, dikiş bir veya iki taraftan uygulanabilir. Çift taraflı kaynak ile yapı daha güvenilirdir ve şeklini daha iyi tutar. Yalnızca tek bir dikiş varsa, genellikle ürünün şekli bozulur: dikiş "çeker". İki tane varsa, bu kuvvetler telafi edilir.
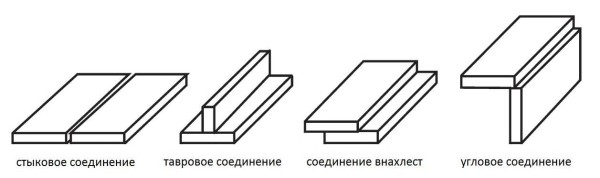
Bağlantı türüne bağlı olarak kaynaklı dikişler alın (uç), tişört, üst üste binme ve filetodur (Resmin boyutunu büyütmek için farenin sağ tuşuyla tıklayın)
Yüksek kaliteli bir kaynak elde etmek için metalin paslı olmaması gerektiğine dikkat etmek imkansızdır. Bu nedenle, kaynak yerleri ön zımparalanır veya pas tamamen kaybolana kadar bir dosya ile işlenir. Ayrıca, gereksinimlere bağlı olarak kenar taşlanır veya taşlanmaz.
Alın eklemi (alın dikişi)
Sac levha veya boru uçlarını birleştirirken alın kaynağı kullanılır. Parçalar, mümkünse, kelepçelerle sıkıca sabitlenmiş olarak aralarında 1-2 mm boşluk olacak şekilde döşenir. Kaynak işlemi sırasında boşluk erimiş metal ile doldurulur.
İnce sac - 4 mm kalınlığa kadar - önceden hazırlık yapılmadan kaynaklanır (pas temizleme sayılmaz, zorunludur). Bu durumda sadece bir tarafta pişirin.4 mm'den itibaren parça kalınlığı ile dikiş tek veya çift olabilir, ancak fotoğrafta gösterilen yöntemlerden biri kullanılarak kenar sızdırmazlığı gereklidir.
- 4 mm'den 12 mm'ye kadar parça kalınlığında dikiş tek olabilir. Daha sonra kenarlar herhangi bir şekilde temizlenir. 10 mm'ye kadar kalınlıkta tek taraflı hazırlık yapmak daha uygundur ve daha kalın parçalar daha sık V harfi şeklinde sıyrılır. U şeklindeki sıyırma işlemi daha zordur, bu nedenle daha az kullanılır. 6 mm'den fazla kalınlıkta kaynak kalitesi için gereklilikler arttırılırsa, her iki tarafta sıyırma ve bir ve diğer tarafta çift dikiş gereklidir.
- 12 mm uç kalınlığında metal kaynak yaparken kesinlikle çift dikişe ihtiyaç vardır, böyle bir tabakayı bir tarafta ısıtmak imkansızdır. X harfi şeklinde iki taraflı kırpma. Böyle bir kalınlıkta, kenarların V veya U şeklinde kırpılması kârsızdır: doldurmak için birkaç kat daha fazla metale ihtiyaç duyarlar. Bu nedenle elektrot tüketimi artar ve kaynak hızı önemli ölçüde azalır.
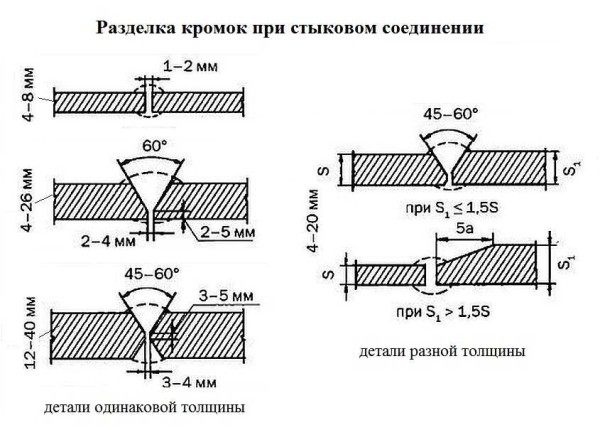
Parçaları uç uca birleştirirken metal kenarları kesmek (Resmin boyutunu büyütmek için üzerine sağ tıklayın)
Bununla birlikte, büyük kalınlıktaki metalin tek taraflı kesim ile pişirilmesine karar verilirse, dikişi birkaç geçişte doldurmak gerekecektir. Bu tür dikişlere çok katmanlı denir.Bu durumda dikişin nasıl kaynaklanacağı aşağıdaki şekilde gösterilmiştir (sayılar, kaynak sırasında metal katmanların döşenme sırasını gösterir).
İnce metalin invertör kaynak makinesi ile kaynaklanması hakkında buradan bilgi edinin.
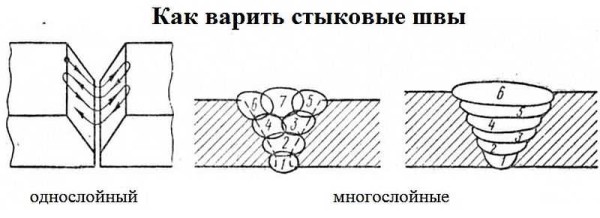
Bir popo dikişi nasıl pişirilir: tek katmanlı ve çok katmanlı (Resmin boyutunu artırmak için üzerine sağ tıklayın)
Tur eklemi
Bu tip bir bağlantı, 8 mm kalınlığa kadar sac metallerin kaynağında kullanılır. Çarşafların arasına nem girmemesi ve korozyon olmaması için her iki taraftan kaynatın.
Örtüşme dikişi yaparken, elektrotun doğru eğim açısını seçmek gerekir. Yaklaşık 15-45 ° olmalıdır. Ardından güvenilir bir bağlantı elde edilir. Bir yönde veya başka bir yönde saptırıldığında, erimiş metalin kütlesi eklemde değil, yan taraftadır, eklemin mukavemeti önemli ölçüde azalır veya parçalar hiç bağlı kalmaz.
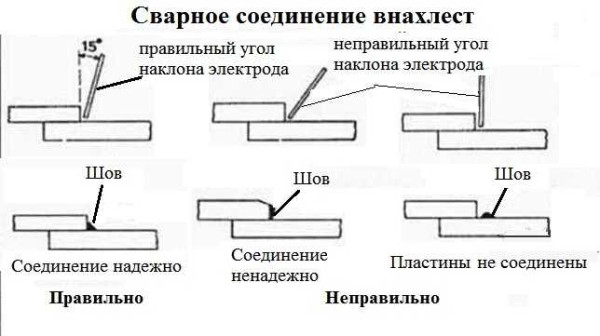
Örtüşen kaynak yaparken elektrot nasıl doğru şekilde tutulur (Resmi büyütmek için üzerine sağ tıklayın)
T ve köşe bağlantısı
Kaynakta T-eklemi "T" harfi, köşe - "G" harfidir. T-ek yeri bir veya iki dikişli olabilir. Kenarlar da kesilebilir veya kesilmez. Kenarın kesilmesi ihtiyacı, kaynak yapılacak parçaların kalınlığına ve dikiş sayısına bağlıdır:
- 4 mm'ye kadar metal kalınlığı, tek dikiş - kenar işlemesiz;
- 4 mm'den 8 mm'ye kadar kalınlık - kenar işlemesiz çift dikiş;
- 4 mm'den 12 mm'ye kadar - bir tarafta oluklu tek dikiş;
- 12 mm'den itibaren kenar iki taraftan kesilir ve iki dikiş de yapılır.
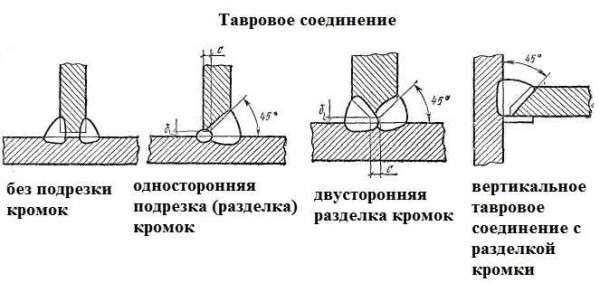
Kaynak türleri: Kenarları kesen ve kesmeyen T-bağlantısı
Köşe kaynağı T bağlantısının bir parçası olarak görülebilir. Buradaki öneriler tamamen aynıdır: ince metal, kesme kenarları olmadan kaynaklanabilir, daha büyük kalınlık için bir parçayı bir veya iki taraftan çıkarmanız gerekir.
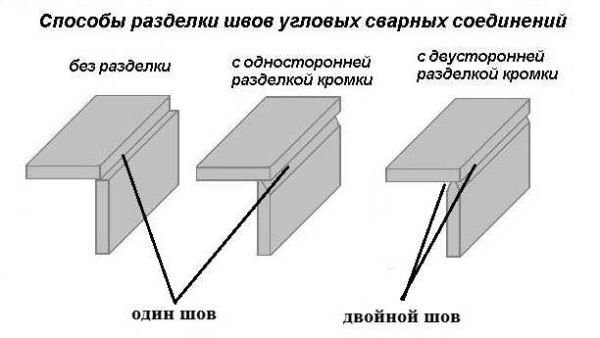
Köşe bağlantısı için metal nasıl hazırlanır (bir veya iki dikişli)
Köşe ve T-bağlantılarının bazen her iki tarafta (iki dikiş) kaynaklanması gerekir. Böyle bir dikişi düzgün bir şekilde kaynaklamak için, parçalar metal düzlemler aynı açıda olacak şekilde döndürülür. Fotoğrafta bu yöntem "bir teknede" imzalanmıştır. Bu, özellikle kaynak yapmaya yeni başlayanlar için elektrot hareketlerini hesaplamayı kolaylaştırır.
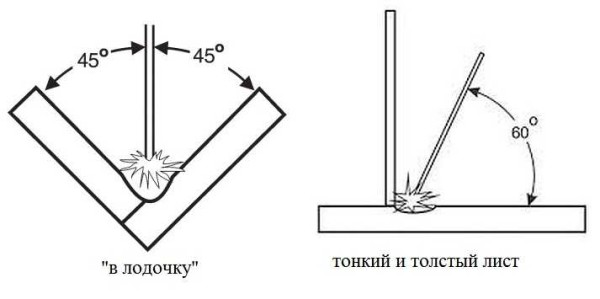
Bir dikiş nasıl pişirilir: "bir teknede" ve farklı kalınlıktaki metalleri birleştirirken
İnce ve kalın metali bağlarken, elektrotun eğim açısı farklı olmalıdır - daha kalın kısma yaklaşık 60 °. Bu konumda, ısıtmanın çoğu üzerinde olacak, ince metal yanmayacak, bu da eğim açısı 45 ° ise meydana gelebilir.
Kaynak köşe kaynakları
Köşe kaynaklarında kaynak yaparken elektrodun konumunu ve hareketini gözlemleyin. İyi doldurulmuş bir dikişe sahip olmalısınız. Parçaları kaynak yapmak için "tekneye" koyarsanız bunu uygulamak daha kolaydır, ancak bu her zaman böyle değildir.
Alt düzlem yatay olarak yerleştirilmişse, genellikle dikey düzlemde ve ayrıca köşede çok az metal olduğu ortaya çıkar: istiflenir. Bu, elektrot, yan yüzeylerinin yakınına göre daha kısa bir süre köşenin üst kısmındaysa olur. Elektrot ucunun hareketi tek tip olmalıdır. İkinci neden, elektrotun çok büyük çapının, aşağı inip eklemin normal şekilde ısınmasına izin vermemesidir.
Bu kusurun ortaya çıkmasını önlemek için ark yatay bir yüzeyde ("A" noktasında) elektrotu dikey yüzeye hareket ettirerek ateşlenir ve ardından dairesel bir hareketle yerine geri döndürülür. Elektrot eklemin üzerindeyken 45 ° 'lik bir eğime sahiptir, yukarı hareket ettikçe açı biraz azalır (soldaki resimdeki resim), yatay bir yüzeye hareket ederken açı artar. Bu teknikle dikiş eşit şekilde doldurulacaktır.
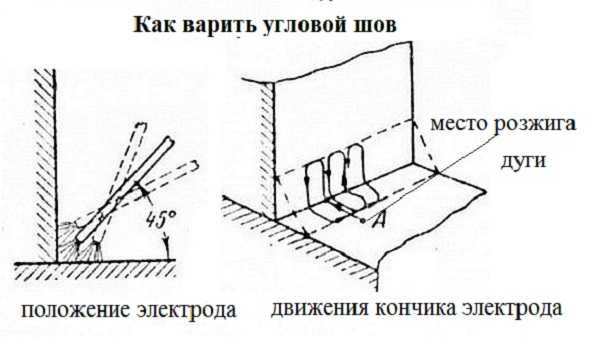
Köşe kaynağı - elektrot konumu ve hareketi
Köşe bağlantılarını kaynak yaparken, her üç noktada (yanlarda ve merkezde) elektrot için harcanan sürenin aynı olduğundan emin olun.
İnverter kaynak makineleri için elektrot seçimini buradan okuyun.
Uzayda konum
Farklı bağlantı türlerine ek olarak, dikişler uzayda farklı şekillerde yerleştirilebilir. Alt konumdalar. Bu, kaynakçı için en rahat olanıdır. Bu, kaynak havuzunu kontrol etmenin en kolay yoludur. Diğer tüm pozisyonlar - yatay, dikey ve üstten dikiş - bazı kaynak teknikleri bilgisi gerektirir (bu tür dikişlerin nasıl kaynaklanacağını aşağıda okuyun).
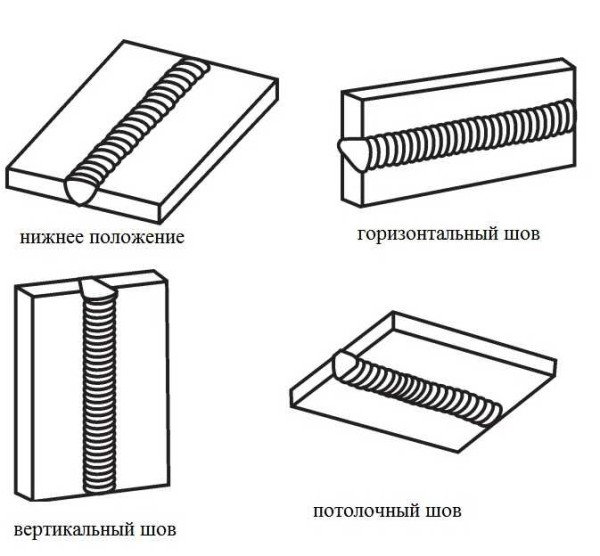
Uzaydaki konuma göre kaynak türleri: dikey yatay, tavan
Bir dikiş nasıl pişirilir
Alt konumda kaynak yaparken, acemi bir kaynakçı için bile zorluk çıkmaz. Ancak diğer tüm hükümler teknoloji bilgisi gerektirir. Her pozisyon için öneriler var. Her bir kaynak türünü yapma tekniği aşağıda tartışılmıştır.
Dikey dikişlerin kaynağı
Dikey konumda parçalar kaynak yaparken, erimiş metal yerçekiminin etkisi altında aşağı kayar. Damlacıkların çıkmasını önlemek için daha kısa bir ark kullanın (elektrotun ucu kaynak havuzuna daha yakındır). Bazı ustalar, elektrotlar izin verirse (yapışmazsa), genellikle onları parça üzerinde destekler.
Derz tipine ve kaynak yapılacak parçaların kalınlığına göre metal hazırlama (kesme kenarları) yapılır. Daha sonra, belirli bir pozisyonda sabitlenirler ve kısa enine dikişlerle birkaç santimetrelik bir adımla - "çiviler" ile bağlanırlar. Bu dikişler parçaların hareket etmesini engeller.
Dikey dikiş, yukarıdan aşağıya veya aşağıdan yukarıya pişirilebilir. Aşağıdan yukarıya doğru çalışmak daha uygundur: ark, kaynaklı havuzu yukarı doğru iterek aşağı düşmesini engeller. Bu şekilde kaliteli bir dikiş yapmak daha kolaydır.
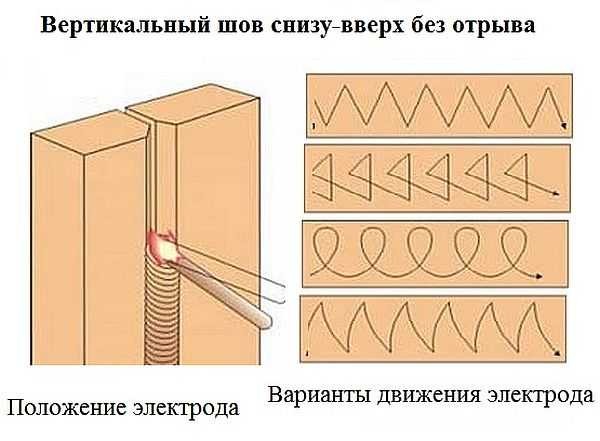
Aşağıdan yukarıya doğru bir dikey dikiş nasıl kaynaklanır: elektrot konumu ve olası hareketler
Bu video, elektrotun aşağıdan yukarıya doğru yırtılmadan hareketi ile elektrik kaynağı ile dikey bir dikişin nasıl düzgün şekilde kaynaklanacağını gösterir. Kısa rulo tekniği de gösterilmiştir. Bu durumda, elektrotun hareketleri yatay yer değiştirme olmadan sadece yukarı ve aşağı meydana gelir, dikiş neredeyse düzdür.
Ark ayrımıyla dikey konumda parçaları bağlamak mümkündür. Acemi kaynakçılar için bu daha uygun olabilir: ayırma süresi boyunca metalin soğuması için zaman vardır. Bu yöntemle elektrodu, kaynaklı kraterin çıkıntısına dayandırmak bile mümkündür. Daha kolay. Hareketlerin paterni, neredeyse hiç ayrılmadan aynıdır: bir yandan diğerine, döngüler veya "kısa yuvarlanma" - yukarı ve aşağı.
Dikey bir dikişi ayırma ile nasıl kaynak yapılır, sonraki videoya bakın. Aynı eğitim videosunda, mevcut kuvvetin dikiş şekli üzerindeki etkisi gösterilmektedir. Genel olarak, akım bu tip elektrot ve metal kalınlığı için önerilenden 5-10 A daha az olmalıdır. Ancak videoda gösterildiği gibi, bu her zaman doğru değildir ve deneysel olarak belirlenir.
Bazen dikey bir dikiş yukarıdan aşağıya kaynatılır. Bu durumda, ark ateşlenirken elektrodu kaynak yapılacak yüzeylere dik tutun. Bu pozisyonda ateşledikten sonra metali ısıtın, ardından elektrodu indirin ve bu pozisyonda pişirin. Dikey bir dikişi yukarıdan aşağıya kaynaklamak pek uygun değildir, kaynak havuzunun iyi kontrol edilmesini gerektirir, ancak bu şekilde iyi sonuçlar elde edebilirsiniz.
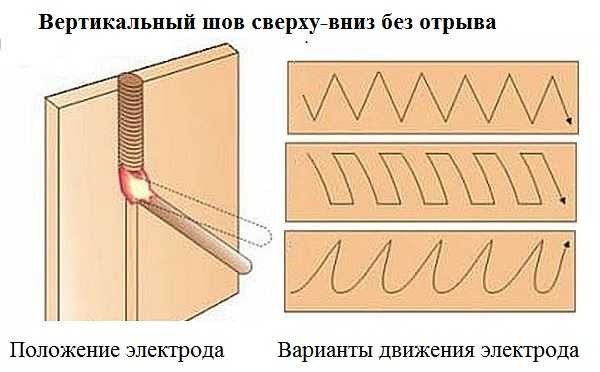
Dikey bir dikiş yukarıdan aşağıya elektrik kaynağı ile nasıl kaynaklanır: elektrotun konumu ve ucunun hareketi
Yatay bir dikiş nasıl pişirilir
Dikey bir düzlemde yatay bir dikiş sağdan sola veya soldan sağa yapılabilir. Fark yok, kim daha uygunsa öyle yemek yapıyor. Dikey bir dikiş kaynağı yaparken olduğu gibi, küvet aşağı doğru eğilimli olacaktır. Bu nedenle, elektrodun eğim açısı yeterince büyüktür. Hareket hızına ve mevcut parametrelere bağlı olarak seçilir. Önemli olan, banyonun yerinde kalmasıdır.
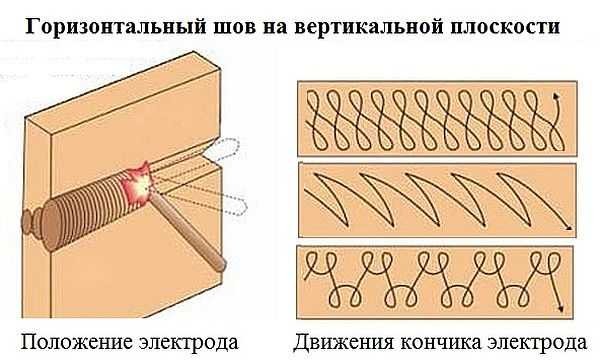
Yatay dikişlerin kaynağı: elektrot konumu ve hareketi
Metal aşağı akarsa, metali daha az ısıtarak seyahat hızını artırın. Başka bir yol da ark kırmaları yapmaktır. Bu kısa aralıklarda metal biraz soğur ve süzülmez. Ayrıca amperajı biraz düşürebilirsiniz. Tüm bu önlemleri aynı anda değil, yalnızca aşamalı olarak uygulayın.
Aşağıdaki video, metalin yatay konumda nasıl düzgün şekilde kaynaklanacağını göstermektedir. Videonun ikinci kısmı dikey dikişlerle ilgili.
Tavan dikişi
Bu tip kaynaklı bağlantı en zor olanıdır. Yüksek beceri ve kaynak havuzunun iyi kontrolünü gerektirir. Bu dikişi tamamlamak için elektrot tavana dik açılarda tutulur. Ark kısadır, hareket hızı sabittir. Dikişi genişleterek temelde dairesel hareketler gerçekleştirilir.
Kaynaklı dikişlerin temizlenmesi
Kaynak işleminden sonra metal yüzeyde kireç sıçraması, metal damlaları ve cüruf kalır. Dikişin kendisi genellikle dışbükeydir ve yüzeyin üzerinde çıkıntı yapar. Tüm bu dezavantajlar ortadan kaldırılabilir: temizlenebilir.
Kaynak sonrası dikişlerin temizlenmesi aşamalı olarak yapılır. İlk aşamada bir keski ve bir çekiç yardımı ile yüzeyden kireç ve cüruf dökülür. İkincisi, gerekirse dikiş karşılaştırılır. Burada bir alete ihtiyacınız olacak: metal için taşlama diski ile donatılmış bir öğütücü. Yüzeyin ne kadar pürüzsüz olması gerektiğine bağlı olarak, farklı tane büyüklükleri kullanın.
Bazen plastik metalleri kaynaklarken kalaylama gerekir - kaynağı ince bir erimiş kalay tabakasıyla kaplayın.
Kaynaklardaki kusurlar
Başlangıç seviyesindeki kaynakçılar, kusurlara yol açan dikişler yaparken sıklıkla hatalarla karşılaşırlar. Bazıları kritik, bazıları değil. Her durumda, daha sonra düzeltmek için hatayı tanımlayabilmek önemlidir. Yeni başlayanlar arasında en yaygın görülen kusurlar eşit olmayan eklem genişliği ve eşit olmayan doldurmadır. Bu, elektrot ucunun düzensiz hareketleri, hareketlerin hızı ve genliğindeki değişiklikler nedeniyle olur. Tecrübe kazandıkça bu eksiklikler gittikçe daha az fark edilir hale gelir, bir süre sonra tamamen ortadan kalkar.
Diğer hatalar - arkın amperajını ve büyüklüğünü seçerken - dikiş şekline göre belirlenebilir. Bunları kelimelerle anlatmak zor, tasvir etmek daha kolay. Aşağıdaki fotoğraf, şeklin ana kusurlarını göstermektedir - alttan kesmeler ve düzensiz doldurma, bunlara neden olan nedenler açıklanmıştır.
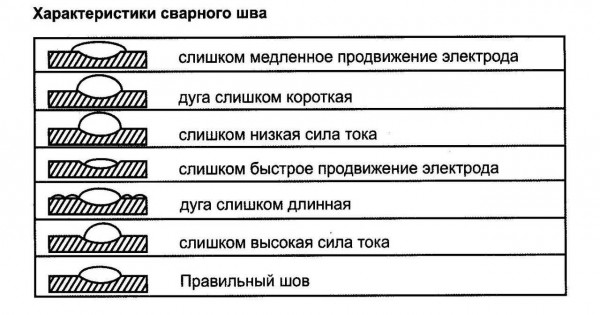
Kaynak yaparken oluşabilecek hatalar
Penetrasyon eksikliği
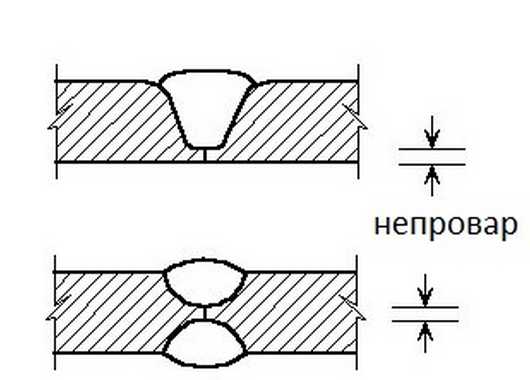
Acemi kaynakçıların yaptığı hatalardan biri: füzyon eksikliği
Bu kusur, parçaların eklemlerinin eksik doldurulmasından ibarettir. Bu dezavantajın, eklemin gücünü etkilemesi nedeniyle düzeltilmesi gerekmektedir. Ana sebepler:
- yetersiz kaynak akımı;
- yüksek hareket hızı;
- yetersiz kenar hazırlığı (kalın metalleri kaynak yaparken).
Akımı ayarlayarak ve ark uzunluğunu azaltarak ortadan kaldırılır. Tüm parametreleri doğru seçtikten sonra bu fenomenden kurtulurlar.
HAKKINDA ev ve yazlık evler için bir invertör kaynak makinesi seçmek için burayı okuyun.
Alttan kesme
Bu kusur, metal üzerindeki dikiş boyunca bir oluktur. Genellikle ark çok uzun olduğunda ortaya çıkar. Dikiş genişler, ısıtma için ark sıcaklığı yeterli değildir. Kenarlardaki metal hızla katılaşır ve bu olukları oluşturur. Daha kısa bir ark ile veya akım gücünü yukarı doğru ayarlayarak "işlenir".
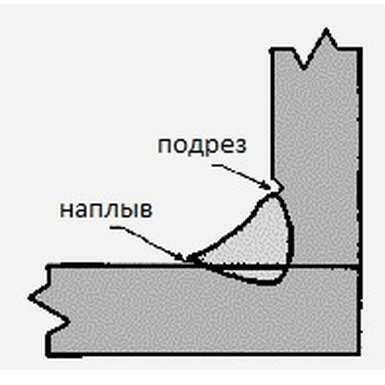
Köşe kesik
Açılı veya T-eklemi ile, elektrotun dikey düzleme daha doğru yönlendirilmesi nedeniyle bir alt kesim oluşur. Sonra metal aşağı akar, tekrar bir oluk oluşur, ancak başka bir nedenle: dikişin dikey kısmının çok fazla ısınması. Akımı azaltarak ve / veya ark kısaltarak ortadan kaldırılır.
Yanmak
Bu, kaynaktaki bir açık deliktir. Ana sebepler:
- çok yüksek kaynak akımı;
- yetersiz seyahat hızı;
- kenarlar arasında çok fazla boşluk.
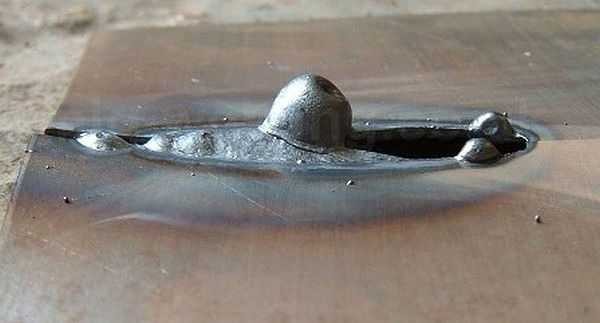
Kaynak yaparken yanmaya benziyor
Düzeltme yöntemleri açıktır - optimum kaynak modunu ve elektrot hareketinin hızını seçmeye çalışıyoruz.
Gözenekler ve sarkma
Gözenekler, birbirine zincirlenebilen veya tüm dikiş boyunca dağılabilen küçük delikler gibi görünür. Bağlantının gücünü önemli ölçüde azalttığı için kabul edilemez bir kusurdur.
Gözenekler belirir:
- kaynaklı havuzun yetersiz korunması durumunda, aşırı miktarda koruyucu gaz (düşük kaliteli elektrotlar);
- kaynak bölgesinde koruyucu gazları ve oksijeni saptıran bir hava akımı erimiş metale girer;
- metal üzerinde kir ve pas varlığında;
- yetersiz kanal açma.
Yanlış seçilmiş modlar ve kaynak parametreleri ile dolgu telleri ile kaynak yaparken sarkma görünüyor. Ana parçaya bağlı olmayan uyuşmuş metali temsil ederler.

Kaynaklı dikişlerin ana kusurları
Soğuk ve sıcak çatlaklar
Metalin soğuması sırasında sıcak çatlaklar oluşur. Dikiş boyunca veya boyunca yönlendirilebilir. Bu tür bir dikiş için yüklerin çok yüksek olduğu durumlarda, soğuk dikişler zaten soğuk bir dikiş üzerinde görünür. Soğuk çatlaklar, kaynaklı eklemin tahrip olmasına yol açar. Bu eksiklikler ancak yeniden kaynak yapılarak giderilebilir. Çok fazla kusur varsa, dikiş kesilir ve tekrar uygulanır.
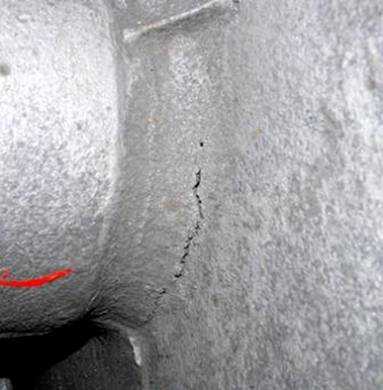
Soğuk çatlaklar ürün arızasına neden olur
Merhaba. İyi makale, her şey ayrıntılı. Tavan dikişi en zor olanıdır.