Aerated concrete blocks: sizes, pros and cons, characteristics
The past century has brought us a lot of new building materials. One of them is aerated concrete. This is a porous type of concrete, which is also called aerated concrete. The presence of air-filled pores made the material lightweight and warm. As a result, it is used both for the construction of walls and partitions, and for insulation. Low weight allows you to vary the size of aerated concrete blocks from small in width, more like slabs - for interior partitions, to wide - for external walls.
The content of the article
What are aerated concrete blocks
Aerated concrete is a material that is obtained from a mixture of cement and sand to which reagents are added, which, when interacting with cement, form foam. Powdered aluminum or a paste from it is used as reagents for aerated concrete. As a result of the reaction of aluminum powder and cement (or lime), pores are formed in concrete - air bubbles evenly distributed throughout the volume. The bubbles are encased in a binder - cement or lime. Such concrete is called cellular or lightweight.
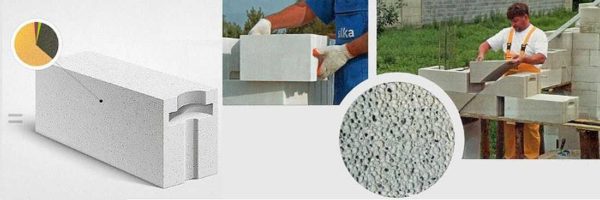
Aerated concrete blocks - building material for the construction of load-bearing and non-loaded walls and partitions
General principles of production
The peculiarity of aerated concrete is that the pores are closed, which reduces the water absorption of the material. It is, of course, more than that of ordinary concrete, but not so critical. The standard defines the area of operation - external and internal walls and partitions in conditions of normal humidity or at humidity no higher than 60% in one GOST and 70% in another.
During production, dry components are first mixed, to which water is then added. As a result of the reaction, the composition "rises". The reaction proceeds to the initial hardening of the binder. Then the aerated concrete is removed from the molds, cut into blocks or slabs of the desired size. Finished products are sent to ripen - to gain commercial strength. There are two types of aerated concrete ripening:
- Autoclave. The blocks are sent to special chambers where they are treated with steam. Increased pressure is created in the chambers. Such processing speeds up the curing process. In terms of quality, autoclave blocks are better: uniform moistening throughout the entire depth gives the material greater strength. But autoclaved aerated concrete costs more: additional equipment, additional energy costs for processing. But for building a house, it is better to buy an autoclaved one.
- Non-autoclave. The blocks are simply laid in the open air and waited for the concrete to gain commercial strength. This is the simplest option, but no one guarantees the quality. According to the technology, the blocks are dried in drying chambers.
Depending on the amount of reagent, aerated concrete can have different density and strength. The more durable ones have fewer pores, the walls of the bubbles are thicker. Such brands are used for the construction of walls.
There are brands of aerated concrete in which there are a lot of air bubbles, their walls are thin. Such blocks and slabs are used for insulation. In general, the material itself has very good thermal insulation characteristics, and it is also easy to process. The presence of a large number of bubbles leads to the fact that the mass of porous concrete is very small. This allows you to make large-format blocks, which significantly speeds up the process of wall erection. And even with large blocks, you can work alone.
Types and types of aerated concrete
Different types of binder can be used in the production of aerated concrete. Also, various mineral components can be added to the material. The name must change depending on the binder and additives. This is spelled out in the GOST.
- Aerated concrete. The binder is cement, and Portland cement is not less than 50%. The best gas blocks are obtained from this material.
- Silicate concrete. A mixture of cement and lime. Boiling lime is at least 50%, cement - 15% by weight, the rest can be additives - slag or gypsum. Silicate gas blocks can be distinguished by their white color. On a cement binder, they are gray.
- Slag and gas concrete. If it contains slag in an amount of more than 50% by weight. The second component of the binder can be cement, lime.
- Zologazobeton. If the highly basic ash is 50% of the binder by weight or more.
It is these names that should be present in the marking and name of the material. They can also use not only quartz sand as a filler, but also ash (waste from thermal power plants), waste generated in the manufacture of ferroalloys, ore beneficiation and other technological processes.
Pros and cons of gas blocks
Gas blocks are an excellent building material. They are easy to handle. You can saw them with an ordinary hand hacksaw for metal, they can be drilled without problems. When using blocks of sufficient density, fasteners are normally twisted in them. The material does not burn and does not support combustion. Lightweight, warm, durable, breathable.
Pros of gas blocks:
- High strength with low weight. Autoclaved aerated concrete has sufficient strength so that a two-three-story mansion can be built from it. At the same time, the weight is low. This means that there will be less load on the foundation, which reduces the cost of its arrangement.
- Low weight of aerated concrete block. For the construction of walls, blocks with a width of 200 mm are usually used, strength grade D500 or D600. Even gas blocks of this size - of considerable width - weigh from 12 to 16 kilograms.
- Excellent thermal insulation properties. According to thermal engineering calculations, a wall made of gas blocks 200 mm thick has the same heat resistance as a brick wall 60-70 cm thick. Despite the fact that it has several times less weight, the cost of building a house is much lower. There are also such names for this material as a heat block, a heat gas block, etc.
- High geometry accuracy. If the blocks do not differ in size, laying is easy. But this parameter depends very much on the manufacturer.
- Moisture resistance and frost resistance. Autoclave gas blocks have good moisture resistance. These figures are much lower than those of bricks, but they are more than enough for building a house.
With all its advantages, the gas block is not ideal. Leaving the walls without finishing is not worth it. But also home decoration from aerated concrete must be correct. The material is breathable and hygroscopic. To prevent moisture from being trapped inside, it is necessary to correctly select the vapor permeability of the finishing materials.
Disadvantages of aerated concrete blocks
Disadvantages of aerated concrete are a consequence of its advantages. For example, ease of handling. When building is good. But it is also easy to cut a passage in the wall from aerated concrete with a chainsaw. This is used by some attackers. The way out is to make a "burglar-proof" finish, for example, brick the house... There are other disadvantages of the gas block:
- Aerated concrete is fragile, does not hold bending loads poorly. The problem is solved by the device of reinforcing belts. But it is important that there is no foundation subsidence.
- When laying gas blocks, special glue is used, which costs a lot. The plus is that with good geometry of the blocks, its consumption is very small - the seams are made by 3 mm.
- If built from blocks containing lime, it quickly corrodes the reinforcement. The problem is solved by using polymer, not metal reinforcement.
- When using gas blocks of low density, special fasteners are needed.
The material is not bad, but you need to really evaluate the pros and cons of gas blocks. You can build a house of permanent residence from them without special fears. For the construction of a bath, aerated concrete blocks are not suitable, as they are too hygroscopic. It is better not to use them for the construction of a house in the country - the low frost resistance of the material will lead to the fact that it will begin to quickly collapse. Is that the temperature in the house will be constantly maintained above zero, and the walls will be well insulated.
Specifications
The main characteristics of any building material are density and compressive strength. It is they who are established by GOST 31359-2007, which describes the requirements for autoclaved aerated concrete.
The compressive strength of the aerated concrete block can be as follows: B0.35; B0.5; B0.75; B1.0; B1.5; B2.0; B2.5; B3.5; AT 5; B7.5; AT 10 O'CLOCK; B12.5; B15; B17.5; IN 20. This indicator characterizes the load that the material can withstand without destruction. The higher the number, the more durable the material.
The second important parameter is the average density. They are related to compressive strength. The higher the density of the material, the greater the load it can bear. So, in essence, both characteristics describe the strength or load-bearing capacity of materials. Just from different sides. For a gas block, the average density can be from D200 to D1200.
Depending on these characteristics, aerated concrete blocks are divided into:
- Structural. For the construction of load-bearing walls and partitions. Specifications B3.5 and above, D700 and above.
- Thermal insulation and construction. For load-bearing and non-stressed walls and partitions with a simultaneous improvement in thermal performance. The required load-bearing capacity of the walls is gained due to the greater thickness. This category includes blocks and slabs with a compressive strength of at least B1.5, and a density of not higher than D700.
- Heat insulating. To reduce heat loss through walls. Strength grade - not higher than D400, density not lower than B0.35. The lower the density, the better the thermal insulation characteristics.
The brand of frost resistance is also determined - the number of defrost / freeze cycles that the material can withstand without changing its properties. This parameter is denoted by the Latin letter F and numbers, which indicate the number of cycles. For autoclaved aerated concrete, the following frost resistance grades are determined: F15, F25, F35, F50, F75, F100. The minimum value of frost resistance for aerated concrete blocks of the outer walls is F25, the inner ones - F15.
Dimensions of aerated concrete blocks according to GOST 31360-2007 and 21520-89
As often happens, several normative documents are in force at once, which creates a certain confusion in the labeling. In addition, the dimensions of aerated concrete blocks are also determined by these standards in different ways. The older standard prescribes precise values in millimeters for the length, width and height of a block. It also introduces differences for mortar or glue masonry. On the mortar, the seam is larger, the size of the blocks is smaller. For gluing, the thickness of the seam is less, the blocks are larger.
The block size itself is encoded in Roman numerals. This is, of course, inconvenient. You must remember the correspondence or have a correspondence table with you. In addition, the increased demands on the energy efficiency of houses have led to the fact that aerated concrete is placed only on glue. Cement mortar is not used, since it is a cold bridge in the masonry, thereby impairing the general characteristics of the wall. Example of marking according to the old standard: I-IN2.5D500F35-2.This means that the block is of the first standard size (188 * 300 * 588 mm), compression strength B2.5, average density D500 and frost resistance F35, accuracy category 2.
The new GOST simply introduces two concepts: aerated concrete block and slab. Maximum sizes are determined for each of them. The exact dimensions are not determined.
The new standard is easier to mark. Block dimensions in millimeters should be indicated. For example, Block I / 600 × 300 × 200 / D500 / B2.5 / F25. Here the category (the permissible error in dimensions is indicated by the Roman numeral I or II) has been moved to the beginning, the order of the characteristics has been changed, but their list remains the same.
Limit deviation category
Both standards prescribe possible deviations in size and defects in the form of violation of rectangularity, curvature of edges and edges, chips. These defects affect the block category. Previously, there were three of them: one for glue masonry, two for mortar masonry. The new standard only describes two categories.
In general, the margins are small by both standards. But foam blocks of the first category have greater accuracy. Exact geometry - less expensive glue consumption. But even with a second class material, low consumption can be achieved. True, this will require additional effort and time. The secret is simple - too large blocks are suspended using a conventional planer, adjusting the size.
Types of gas blocks
Construction - wall and partition blocks - made of aerated concrete can be in the form of a parallelepiped with smooth edges or with a formed tongue-and-groove system on the sides. The second option is done if the dimensions of aerated concrete blocks are closer to large ones: with a width of 200 mm. In large blocks, additional holes are often made for ease of portability. It really makes the job easier.
There are also U-shaped blocks for the construction of reinforcing belts. Reinforcement is laid in the recesses formed by the walls of the block, everything is poured with concrete.